
TFT LCDディスプレイの構造
- 液晶パネル (パネル) : これはディスプレイの主要部分であり、画像を表示する役割を果たします。液晶パネルは、液晶セルと呼ばれる液晶層を挟んだ 2 枚のガラス板で構成されています。
- 偏光フィルター:これらのコンポーネントは液晶セルの両側に配置され、セルを通過する光を処理する役割を果たします。
- カラーフィルター: 通常は、密封された液晶セルのガラス板の 1 つ上に製造され、カラー表示に使用されます。
- 薄膜トランジスタアレイ(TFTアレイ) :密封された液晶セルのもう一方のガラス板上に配置され、ディスプレイの駆動に重要な役割を果たします。
- バックライト: TFT-LCD ディスプレイ モジュールの後ろにある光源は、液晶セルを通して可視画像を生成するために必要な光を提供します。
- 外部駆動回路:これらの回路は、入力画像信号を管理して、TFT アレイとバックライトを適切に駆動する役割を担います。

TFT LCDディスプレイの製造工程
- フィルム形成: スパッタリング (SPT) や化学蒸着 (CVD) などの技術により、基板上に複数の層を堆積します。
- フォトリソグラフィー: フォトレジストを塗布、露光、現像して微細構造を形成します。
- エッチング: ウェットエッチングとドライエッチングの方法は、特定の領域を除去することで基板を彫刻します。
- 剥離: パターン形成後、余分な材料を除去して基板を洗浄します。
補助的なプロセス手順:
クリーニング:基板に汚染がないことを確認します。
マーキングと露出:基板のエッジを識別して準備します。
自動光学検査 (AOI):欠陥検査に使用されます。
顕微鏡検査とマクロ検査(Mic/Mac):詳細チェック。
フィルム性能テスト:シート抵抗計、プロファイロメータ、反射計/偏光解析法、フーリエ変換赤外分光法などのツールを使用します。
オープン/ショート (O/S) 電気テスト:回路の導通とショートをチェックします。テスト要素グループ (TEG) 電気テスト: 要素の電気性能をテストします。
アレイの電気テスト:アレイの電気機能を確認します。
レーザー修復:検査結果に応じて欠陥を修正します。
フォトレジストリワーク (PR リワーク):必要に応じてフォトリソグラフィの手順を調整または繰り返します。
フィルムの再加工: 必要に応じてフィルム形成プロセスを変更または改良します。

- OC レイヤー カラーフィルターパターンを保護し、準備します。
- RGBレイヤー コーティング、露光、現像のシーケンスによる形成。
- BM(ブラックマトリックス)レイヤー コントラストを高め、光漏れを制限します。
- PS (フォトスペーサー) レイヤー 画質にとって重要な、基板間の正確なギャップを維持します。
- ITO層 電気伝導とタッチ機能のための透明導電フィルムを追加します。

- ポリイミド (PI) の配向と方向付け: 液晶配向のために PI 層を適用し、配向します。
- ODF(光学ディスプレイフィルム) 視覚効果が向上します。
- 洗浄およびフレームシーラントの塗布:液晶液滴の挿入の準備。
- 液晶注入:液晶をディスプレイ上に正確に注入します。
- TFT と CF のラミネーション: TFT と CF のコンポーネントを結合します。
- UV硬化と熱処理:紫外線と熱処理により液晶を固めて均一に分散させます。
- 切断、電気テスト、エッジの平滑化: 基板の形状を整え、電気チェックを実行し、エッジを平滑化します。
- 偏光板の取り付けと気泡除去: 偏光フィルムを貼り付け、気泡を除去します。必要に応じてやり直しも可能です。

- レーザー切断と電気テスト: 正確な形状と電気的完全性を保証します。
- COG (Chip On Glass) ボンディング、FPC (Flexible Printed Circuit) ボンディングとテスト: 駆動回路の取り付けとテスト。
- 組み立てと電気テスト: すべてのディスプレイ モジュール部品を組み合わせ、最終的な電気テストを実行します。
- エージング:製品の信頼性を確保するための長期電源供給。
- 梱包と発送:完成品を配送用に準備します。

配列セグメントフロー
- G: SiNx (窒化シリコン) で作られたゲート絶縁体は、ゲートと他の層の間に必要な絶縁を提供します。
- I: 電子スイッチングが行われるチャネル層、a-Si (アモルファス シリコン)。
- N: n+ a-Si 層には高濃度のホスフィン (PH3) がドープされています。このドーピングにより、界面の電位障壁が低減され、信頼性の高いデバイス動作に不可欠なオーミック接触が確保されます。

ゲートメタル(AlNd/MoN)

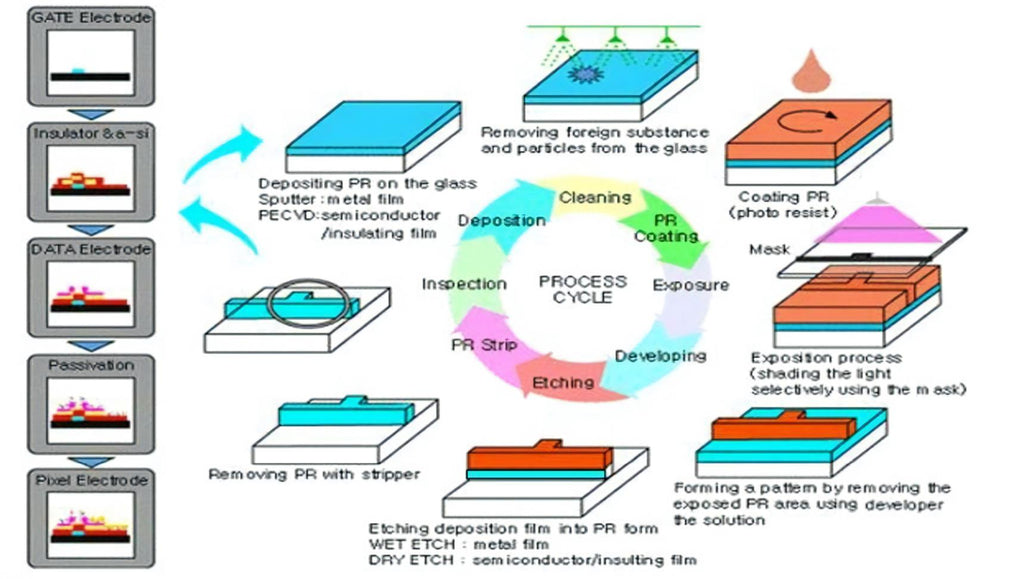
GIN (SiNx / a-Si / n+ a-Si)

S/D 金属 (Mo \Al\Mo)
ソースおよびドレイン電極 (S/D)、データ電極、およびチャネルの形成には、窒化モリブデン (MoN) と純アルミニウム (ソースおよびドレイン用) の積層、S/D 金属層のスパッタリング、S/D フォトリソグラフィ、S/D ウェット エッチング、およびチャネル ドライ エッチングなどの特定の手順が含まれます。これらのプロセスを通じて、TFT のソースおよびドレイン電極、チャネル、およびデータ ラインがガラス基板上に形成されます。この段階で、TFT の構築が完了します。結果として得られる設計とプロセスは次のとおりです。
- S/D スパッタリング: これはソース/ドレイン電極を形成するための重要なステップです。このプロセスでは、基板上に重金属イオンをスパッタリングすることで、金属電極の緻密な層が形成されます。
- PR コーティング前の洗浄: フォトレジストを塗布する前に、基板を洗浄してほこりや残留物を除去して、良好なコーティング結果を確保する必要があります。
- DHP (ホットプレート) : フォトレジストを基板にしっかりと接着させるために、コーティングプロセスの前に基板をホットプレート上で予熱します。
- レジストコーティング: 予熱した基板にフォトレジストの層を塗布します。この層は、後続のパターン形成に使用されます。
- 事前硬化 (SHP) : フォトレジストをコーティングした基板を事前硬化して、フォトレジストをより均一かつ強力にします。
- ステッパー露光: このステップでは、露光量を制御してフォトレジストの特定の領域を硬化させ、目的のパターンを作成します。
- 現像: 露光されたフォトレジストを処理してパターンを明らかにします。
- フォトレジストポストベーキング (HHP) : フォトレジストパターンは、別の加熱プロセスによってさらに硬化され、より顕著になります。これにより、化学的腐食や摩耗に対する耐性も向上します。
- 開発検査: 開発後は、パターンの正確性を確認し、問題を迅速に検出して対処するために詳細な検査が必要です。
- ウェットエッチング: 腐食性の液体を使用して保護されていない領域の材料をエッチングし、回路パターンを形成する化学反応プロセスです。
- チャネル ドライ エッチング: ソースとドレインの間にチャネルが形成されます。このプロセスでは、チャネル領域のシリコンをドライ エッチング技術を使用して必要な形状にエッチングします。
- レジストストリップ:最後に、基板表面を洗浄するために、基板上のフォトレジストを剥離します。
上記の工程を経て、最終的にガラス基板上にTFTのソース/ドレイン電極、データ電極、チャネルが形成されます。
パッシベーション(SiNx)
保護絶縁層とも呼ばれるパッシベーション層 (SiNx) の形成には、ビアとともに、PECVD フィルム形成、フォトリソグラフィー、ビア作成のためのドライエッチングなどの特定の操作が含まれます。これらの手順を経た後、最終的に TFT チャネルの保護絶縁層と導電性ビアがガラス基板上に形成されます。これらの手順の完了後に得られた画像とプロセスは次のとおりです。
2. 塗装前の洗浄 - フォトレジストを塗布する前に基板を洗浄する場所です。
3. ホットプレートでプリベイクする (DHP) - コーティング工程の準備として、ホットプレートを使用して基板を予熱します。
4. フォトレジストコーティング - この段階では、フォトレジストの層が基板上に塗布されます。
5. ソフトベイク (SHP) - フォトレジストでコーティングされた基板は、層を固めるために事前硬化プロセスを経ます。
6. ステッパー露光 - ここでは、ステッパーリソグラフィー技術を使用してフォトレジストを露光し、パターンを形成します。
7. 開発中 - 露光されたフォトレジストが処理されてパターンが現れます。
8. ハードベイク (HHP) - フォトレジストパターンはポストベーク処理によって硬化されます。
9. 現像後の検査 - この段階では、開発された基板を検査してパターンの精度を確認します。
10. ウェットエッチング - 不要な薄膜材料は湿式化学エッチングプロセスによって除去され、回路パターンが作成されます。
11. フォトレジスト剥離 - フォトレジストを除去し、基板の表面を洗浄します。
12. コンタクトホールエッチング (CH エッチング) - 必要なビアはドライエッチングプロセスによって形成されます。
これらは、TFT アプリケーション用の基板を準備する際に必要な詳細な手順であり、アクティブ TFT チャネルの保護と導電性ビアの形成につながります。
透明画素電極ITO(インジウムスズ酸化物)の形成
TFT ディスプレイの透明ピクセル電極の作成は、インジウムスズ酸化物 (ITO) の堆積から始まる高度なプロセスです。関連する段階は精密に設計されており、透明性を実現するために ITO 層をスパッタリングし、その後に複雑なパターンを形成するフォトリソグラフィーを行い、最後にウェットエッチングでピクセル構造を完成させます。この細心の注意を払った一連の作業は、ガラス基板上に完璧に統合されたピクセル電極の形成で終わり、アレイ プロセスの重要な完了を示します。次のワークフローは、プロセス完了後の操作の改良とシーケンスの詳細を示しています。
- ピクセル層堆積(ITOスパッタリング) – 後続のピクセルパターン形成のために、ITO (インジウムスズ酸化物) の透明導電膜を形成します。
- 基板洗浄(レジストコーティング前洗浄) – フォトレジスト材料を塗布する前に基板の純度を確認します。
- 基板予熱(脱水ホットプレート、DHP) – 最適なフォトレジスト接着のために、プリベークステップで基板を準備します。
- レジスト塗布(コーティング) – 基板上に均一なフォトレジスト層を塗布します。
- ソフトベイク(プレキュアSHP) – パターン形成前にフォトレジストを固めるための予備硬化を実施します。
- 精密露光(ステッパー露光) – ステッパーフォトリソグラフィーを使用してフォトレジストを露光し、目的のパターンを作成します。
- パターン開発(開発中) – 露光されたフォトレジストを現像して、複雑なピクセル パターンを明らかにします。
- レジスト硬化(露光後ベーク、ハードベークHHP) – パターン化されたフォトレジストを硬化させてエッチング耐性を向上させます。
- パターン検査(現像後検査) – 開発されたパターンの正確性と整合性を検査します。
- パターン転写(ITOエッチング) – ITO 層をエッチングしてパターンを転写し、ピクセル電極を形成します。
- レジスト除去(ストリップ) – フォトレジストを剥離し、きれいな基板表面を残します。
- パフォーマンス向上(アニーリング) – 薄膜トランジスタの電気特性を向上させるためにコンポーネントをアニールします。
- 品質管理(TEGテスト) – 製造中の品質を監視するために、テスト要素に対して電気テストを実行します。
この合理化されたシーケンスは、最適な電気性能を備えた高品質の TFT ディスプレイの基礎を築きます。

カラーフィルター(CF)プロセス
- ガラス基板: 機械的なサポートを提供する基礎ベース層。
- ブラックマトリックス(BM): 光吸収材料で構成されており、各ピクセルを区別し、ピクセル間の光漏れを最小限に抑えてコントラストを向上させます。
- カラー樹脂層: これらの層は、実際の赤、緑、青のフィルターと同様に、ピクセルの色を決定します。これらは、染色された透明な樹脂材料から作られています。
- オーバーコート層(OC): 色樹脂の上に保護層を重ねて表面を平らにし、フィルターを物理的および化学的損傷から保護します。
- ITO (インジウムスズ酸化物) 電極: この透明導電層により、パネルは電極として動作し、通過する光を制御できるようになります。

- 基板の準備: ガラス基板の清浄度は最も重要であるため、CF の品質を損なう可能性のある不純物を除去するために徹底的な洗浄が行われます。
- ブラックマトリックスの形成: 洗浄した基板にフォトレジスト層を塗布し、フォトリソグラフィーを使用して BM パターンの輪郭を描きます。露光後、未現像領域が現れ、黒色顔料で満たされ、硬化されます。
- カラー樹脂の用途: BM の範囲内で、赤、緑、青のカラー樹脂を各カラー層ごとに異なるフォトリソグラフィー プロセスを使用して連続的に塗布します。コーティングと露光の後、フォトレジストのない領域を現像して樹脂を充填し、硬化させます。
- オーバーコート層の適用: 樹脂カラーの上に OC 層を塗布して保護し、その後の ITO 電極堆積のための滑らかな表面を確立します。
- ITO電極堆積: 透明な ITO 電極は OC 層上にスパッタリングで堆積され、その後パターン化されて電極アーキテクチャが構築されます。
- 検査とテスト: 製造の全過程において、綿密な検査とテストにより CF の品質が確保されます。色の忠実度、均一性、欠陥レベルなどの指標が徹底的に検査されます。
- 統合: 品質保証後、カラーフィルターはTFTアレイや液晶層などのTFT-LCDパネル構成要素と正確に位置合わせされ、ラミネートされます。

CELLセグメントフロー
TFT ディスプレイの「セル」部分における製造プロセスは、おおまかに 4 つの主要な段階に分けられます。アライメント、ボックス化、切断、偏光板の取り付けです。これらの段階の目的と主な手順を、以下に簡単に説明します。
アライメントプロセス
アライメント プロセスの目的は、TFT 基板と CF 基板の両方に透明な PI (ポリイミド) フィルムの層を作成することです。その後の摩擦プロセスを通じて、この層は液晶分子を摩擦の方向に整列させるように作用します。基礎原理をより深く理解するには、関連する文献を参照してください。したがって、この段階では、PI 印刷とラビングという 2 つの主要なプロセスが顕著に表れます。
PI(ポリイミド)印刷
ポリイミド (PI) は、主鎖と側鎖からなる高性能の透明有機ポリマー材料です。塗布して焼成すると、CF および TFT 基板の表面にしっかりと接着します。PI のコーティングには、特殊なグラビア印刷技術が使用されています。主なグラビア印刷プロセスに加えて、PI 印刷には、印刷前の基板洗浄、印刷後の予備焼成、自動光学検査、硬化、必要に応じて PI 再加工プロセスなど、いくつかの補助プロセスが含まれます。
1. PI 前のクリーニング: このステップでは、印刷前に基板を徹底的にクリーニングし、次のステップに備えてほこり、グリース、その他の汚染物質がないことを確認します。
2.PI 印刷:ここでは、PI (ポリイミド) 材料が基板に塗布されます。これは、紙にデザインを印刷するのと似ていますが、「インク」は保護層を形成する特殊な材料である点が異なります。3. 予備ベーキング: これは、PI 層を部分的に乾燥させて基板への適切な接着を確保する予備ベーキング段階と考えてください。
4.PI 検査:この時点で、印刷された層は、塗装された壁の欠陥を検査するのと同様に、汚れ、凹凸、または欠陥がないか厳密に検査されます。
5.PI 再作業:検査中に問題が特定された場合、このステップでは、スケッチの間違いを消すのと同様に、それらの不完全さを修正する必要があります。
6.PI 硬化:最後に、PI 層は、粘土が窯で硬化されるのと同じように、焼成プロセスによって完全に硬化され、強度と耐久性が向上します。
この段階では、超音波洗浄機を使用して基板からほこりや粒子を取り除き、徹底的な洗浄を行います。これにより、次のステップに進む前に基板に汚染物質がないことが保証されます。
2. アライメント:
アライメント フェーズでは、視覚的な要件を満たすように基板の向きを調整します。このプロセスは簡単で、後続の処理のために基板を正しく配置することに重点が置かれています。
3. こする:
擦り付け段階では、ベルベットの布を使用して PI 層を擦ります。この動作により、PI の側鎖が統一された方向に整列し、分子構造が整えられて、望ましい表面特性が実現されます。
4. 擦り合わせ後の超音波洗浄(USC):
研磨後、基材には粒子状物質や残留物が付着している場合があります。研磨後の USC 洗浄によりこれらの残留物が除去され、基材の表面が完璧にきれいになります。このステップは、研磨プロセス中に付着した粒子や残留物を超音波で除去するため、最終製品の品質を維持するために非常に重要です。

ODF(ワンドロップフィル)カプセル化プロセス
1. シーラントと銀ペーストの塗布: UV 硬化型接着剤をシーラントとして使用し、CF および TFT ガラス基板の端に沿って塗布することで、2 つの基板がしっかりと接着され、セルの厚さが定義されます。同時に、銀ペーストを塗布して CF と TFT の共通電極を接続し、電気接続を確保します。
2. 液晶コーティング:シーラントが塗布されたTFT基板に液晶材料を滴下します。液晶材料は表示プロセスにおいて重要な役割を果たし、配列を変更することで通過する光の状態を調整し、ピクセルの色と明るさを制御します。
3. 真空接合:シーラント、銀ペースト、液晶を塗布した CF 基板を真空環境で TFT 基板と接合します。この工程により、気泡の発生を防ぎ、2 つの基板間の隙間のない密着性を確保します。
熱硬化: UV 硬化が完了したら、基板は熱処理を受け、シーラントの接着力をさらに強化します。このステップは、リードの下など、UV 光が完全に届かない領域に特に重点を置き、これらの部品が完全に硬化するようにします。

1.切断
ガラス基板の大きさが一定で製品サイズも多様であるため、1枚のガラス基板上に複数の製品セルを配置し、ダイヤモンドホイールをガラス表面でスライドさせて切断します。通常は切断後に剥離工程がありますが、切断ホイール技術の進歩により、非常に深い切断痕を形成できる技術が開発され、剥離工程が不要になりました。
2.エッジング
ガラスを個々のスクリーンに切断した後、各スクリーンのエッジには多数の微細な亀裂が発生します。これらの亀裂がその後の取り扱い時に衝突して破損するのを防ぐために、エッジ処理が必要です。
3.電気測定
電気測定は、製造中に何度も使用される補助的なプロセスですが、LCD の表示性能をテストするために初めて電気が適用されるため、ここでは特に重要です。テストの原理は単純です。個々の表示ピクセルに電気を適用し、偏光フィルムを通してセルの表示性能を観察します。通常、アレイ テストに使用されるショート バーに電気が通電されます。電気テストの後、基準を満たさないスクリーンは、後の段階で材料が無駄にならないように取り除かれます。
追加の補助プロセスには、切断後の目視検査とエッジング後の清掃が含まれます。
TFTディスプレイモジュールの組み立て工程
TFT ディスプレイ モジュールの組み立てに含まれる主なプロセスには、偏光フィルムの適用、COG および FPC の接着、組み立て、およびさまざまなサポート プロセスが含まれます。以下に、それぞれの詳細な紹介を示します。
1.COGとFPCの接合
COG (Chip on Glass) と FPC (Flexible Printed Circuit) は、回路を接続する方法の代表例です。電極の数が多いため、従来の 1 対 1 の配線接続は困難です。現在の方法では、ガラス上に電極アレイを形成し、対応するアレイを IC/FPC 上に形成し、異方性導電フィルム (ACF) を使用して各 IC/FPC 電極をガラス電極に 1 つずつ接続します。2.偏光フィルムの貼り付け
LCD の動作は偏光に基づいているため、偏光フィルムの取り付けは不可欠なプロセスです。このフィルムは、液晶セルを通過する光を制御して画像を生成します。
3.組み立て
組み立てでは、バックライト、スクリーン、制御回路基板、タッチスクリーンなどのその他のコンポーネントをまとめて、ディスプレイ モジュールを完成させます。これは通常、熟練した技術者によって手作業で行われ、組み立てられたモジュールの品質を確保する上で重要な役割を果たします。
モジュール セグメントには、メイン プロセスに加えて、次のようないくつかの補助プロセスが含まれます。
1.レーザー切断と切断後の電気測定
レーザーを使用して部品を正確に切断した後、電気機能がテストされ、必要な仕様を満たしているかどうかが確認されます。2.接合および接合後の電気測定
COG および FPC 接合プロセスの後には、これらの接続の整合性を確認するために電気テストも実行されます。
3.顕微鏡検査
レーザー切断と接合後、顕微鏡検査(または FPC 接合の場合は自動光学検査 (AOI))を実行して、欠陥や問題がないか確認します。
4.剥離強度試験
IC 接合および FPC 接合後、接合の耐久性を評価するために剥離強度テストが行われます。
5.組み立て後の経年変化
組み立てられたモジュールは、長期的な信頼性を確保するために、電力を供給しながらエージング プロセスを経ます。
6.梱包と発送
モジュールがすべてのテストと検査に合格すると、パッケージ化されて顧客または次の生産段階に出荷されます。

コメントを書く
このサイトはhCaptchaによって保護されており、hCaptchaプライバシーポリシーおよび利用規約が適用されます。