Unser Qualitätsanspruch
Qualitätskontrollsystem
Qualität hat bei der BROWNLN Company oberste Priorität. Wir verfügen über ein engagiertes Qualitätsmanagementteam, moderne Prüfgeräte und ein strenges Qualitätskontrollsystem, um sicherzustellen, dass jedes Produkt, das unser Werk verlässt, unseren hohen Qualitäts- und Zuverlässigkeitsstandards entspricht.
Professionelles Qualitätsmanagement-Team
Wir verfügen über ein professionelles Qualitätsmanagementteam mit Mitgliedern, die über umfassende Branchenerfahrung und Fachkenntnisse verfügen. Sie sind für die Überwachung und Verwaltung der Qualitätskontrollarbeiten während des gesamten Produktionsprozesses verantwortlich und stellen sicher, dass jeder Schritt strengen Qualitätsstandards entspricht. Darüber hinaus nimmt das Team regelmäßig an Schulungen und Weiterbildungen teil, um seine beruflichen Fähigkeiten und Fertigkeiten kontinuierlich zu verbessern.
Strenger Qualitätsprüfungsprozess
Unser Qualitätsprüfungsprozess ist streng und umfassend und umfasst mehrere Inspektionsstufen. Jedes TFT-Modul wird während des Produktionsprozesses mehreren Prüfungen unterzogen, darunter Sichtprüfung, Funktionstests, Umwelt- und Zuverlässigkeitstests, Teilenummern- und Mengenüberprüfung, Datenblattvalidierung und 100 %-Prüfung, sofern erforderlich. Zur Qualitätssicherung befolgen wir außerdem die Stichprobenprüfungen MIL STD 1916 und ANSI/ASQ Z1.4. Nur Produkte, die alle Prüfungen bestehen, können in den nächsten Produktionsschritt übergehen, wodurch die Qualität jedes Produkts sichergestellt wird, das unser Werk verlässt.
Moderne Inspektionsausrüstung
Unser Unternehmen verwendet hochmoderne Inspektionsgeräte, um die Genauigkeit und Zuverlässigkeit jeder Inspektion sicherzustellen. Zu unserer modernen Ausrüstung gehören hochpräzise Maschinen zur automatischen optischen Inspektion (AOI), Geräte zur Funktionsprüfung und Umweltprüfkammern. Durch den Einsatz der AOI-Technologie anstelle einer manuellen Inspektion vermeiden wir menschliche Ermüdung und reduzieren das Risiko menschlicher Fehler erheblich. Durch AOI-Tests weisen unsere Produkte eine Fehlerrate von weniger als 300 PPM auf, was die Qualität und Genauigkeit unserer Produkte erheblich verbessert. Die AOI-Maschinen können winzige Defekte von bis zu 5 μm für Flecken und 50 μm für Fremdkörper erkennen. Sie erkennen auch Mura-Defekte mit einem 2 %-Graubildschirm, Farbdefekte mit geringem Kontrast mit einer Genauigkeit von ±0,0002 und verschiedene andere Defekte wie helle/dunkle Flecken, Linien, Fremdkörper in der Hintergrundbeleuchtung, Anzeigeanomalien, Lichtaustritt am Rand, Farbtemperaturabweichungen und Mura-Defekte.
Umweltüberwachung und Zuverlässigkeitstests
Um die Zuverlässigkeit und Stabilität unserer TFT-Module in verschiedenen Umgebungen sicherzustellen, führen wir umfassende Umweltüberwachungen und Zuverlässigkeitstests durch. Diese Tests umfassen Hochtemperatur- und Hochfeuchtigkeitstests, Niedertemperaturtests, Vibrationstests, Falltests und mehr und simulieren verschiedene extreme Bedingungen, denen das Produkt im realen Einsatz ausgesetzt sein kann. Durch diese Tests können wir garantieren, dass unsere Produkte in allen Arten von Umgebungen gut funktionieren.
Einführung in das Qualitätskontrolllabor
Unser Qualitätskontrolllabor ist mit modernen Prüfgeräten ausgestattet und beschäftigt professionelle Techniker, die für die Durchführung umfassender Qualitätsprüfungen und Analysen von TFT-Modulen verantwortlich sind. Das Labor arbeitet streng nach internationalen Standards, um die Genauigkeit und Zuverlässigkeit aller Testergebnisse zu gewährleisten. Wir erneuern und verbessern unsere Techniken außerdem kontinuierlich, um unsere Testmöglichkeiten und unser Fachwissen zu verbessern.
Unsere Inspektionsgeräte
Unsere Qualitätsprüfausrüstung umfasst sechs vollautomatische Produktionslinien, die jeweils mit Online-Partikel-AOI-Prüfgeräten und automatischen LCM-Defekt-AOI-Prüfsystemen ausgestattet sind. Diese Geräte nutzen hochauflösende Bildgebungstechnologie und fortschrittliche Bildverarbeitungsalgorithmen, um kleine Partikel und Druckstellen auf der Oberfläche des Produkts, einschließlich solcher von FPC/IC-Verbindungen, genau zu erkennen. Sie erreichen außerdem eine 100-prozentige Prüfung der Partikelmenge und Positionsabweichung und stellen so sicher, dass unsere Produkte den höchsten Qualitätsstandards entsprechen. Durch den Einsatz dieser fortschrittlichen Geräte können wir die Qualität und Zuverlässigkeit unserer Produkte gewährleisten und unseren Kunden zuverlässige Produkte bieten.
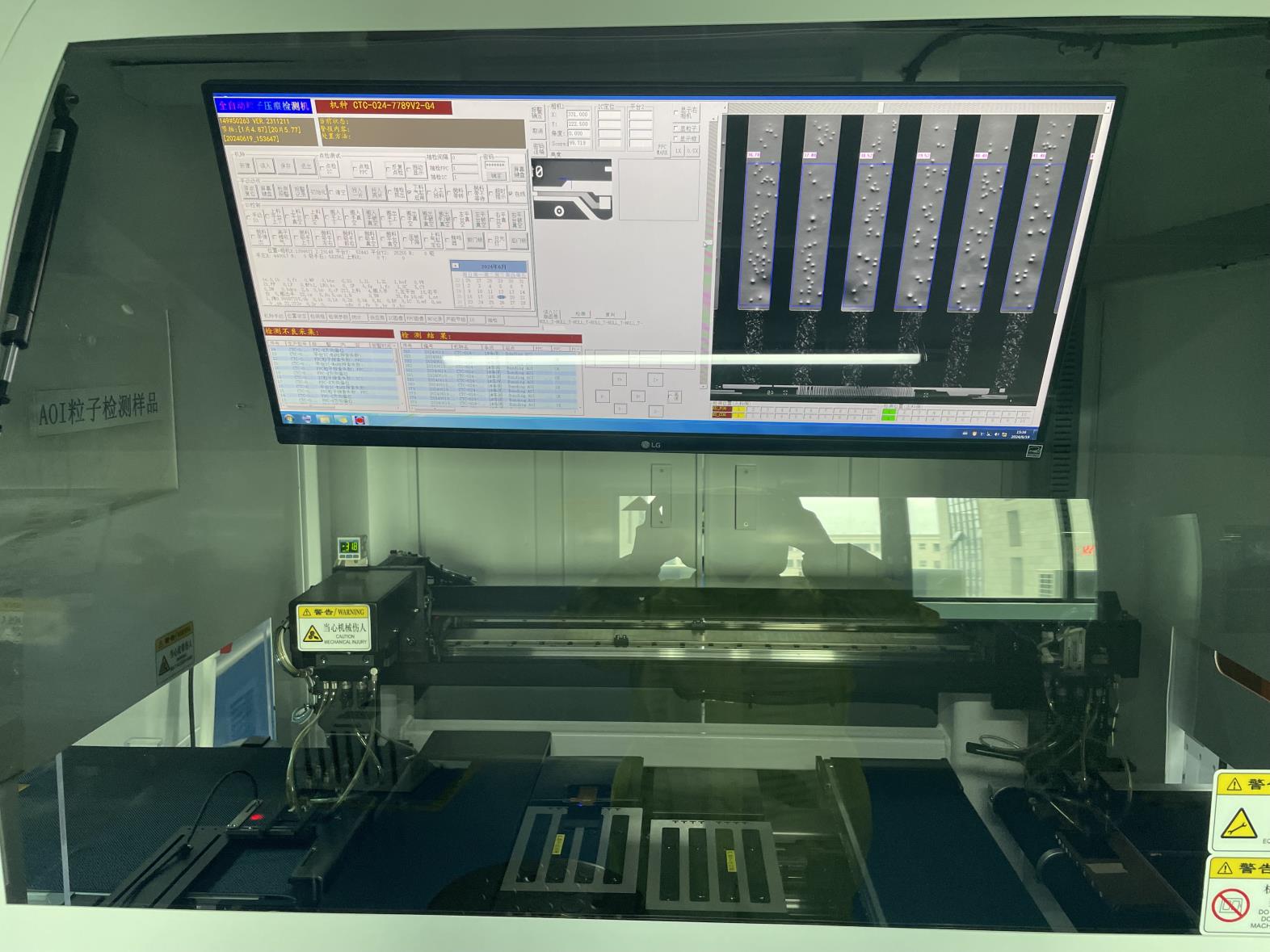
Unsere Inspektionsausrüstung umfasst sechs vollautomatische Produktionslinien mit Online-Partikel-AOI und automatischen LCM-Defekt-AOI-Systemen. Diese fortschrittlichen Geräte erkennen kleine Partikel und Druckstellen auf der Produktoberfläche präzise und erreichen eine 100-prozentige Inspektion der Partikelmenge und Positionsabweichung für alle COG- und FOG-Produkte. Dies gewährleistet höchste Qualitätsstandards für unsere Produkte.
Unsere Inspektionsausrüstung umfasst sechs vollautomatische Produktionslinien mit Online-Partikel-AOI und automatischen LCM-Defekt-AOI-Systemen. Diese fortschrittlichen Geräte erkennen kleine Partikel und Druckstellen auf der Produktoberfläche präzise und erreichen eine 100-prozentige Inspektion der Partikelmenge und Positionsabweichung für alle COG- und FOG-Produkte. Dies gewährleistet höchste Qualitätsstandards für unsere Produkte.
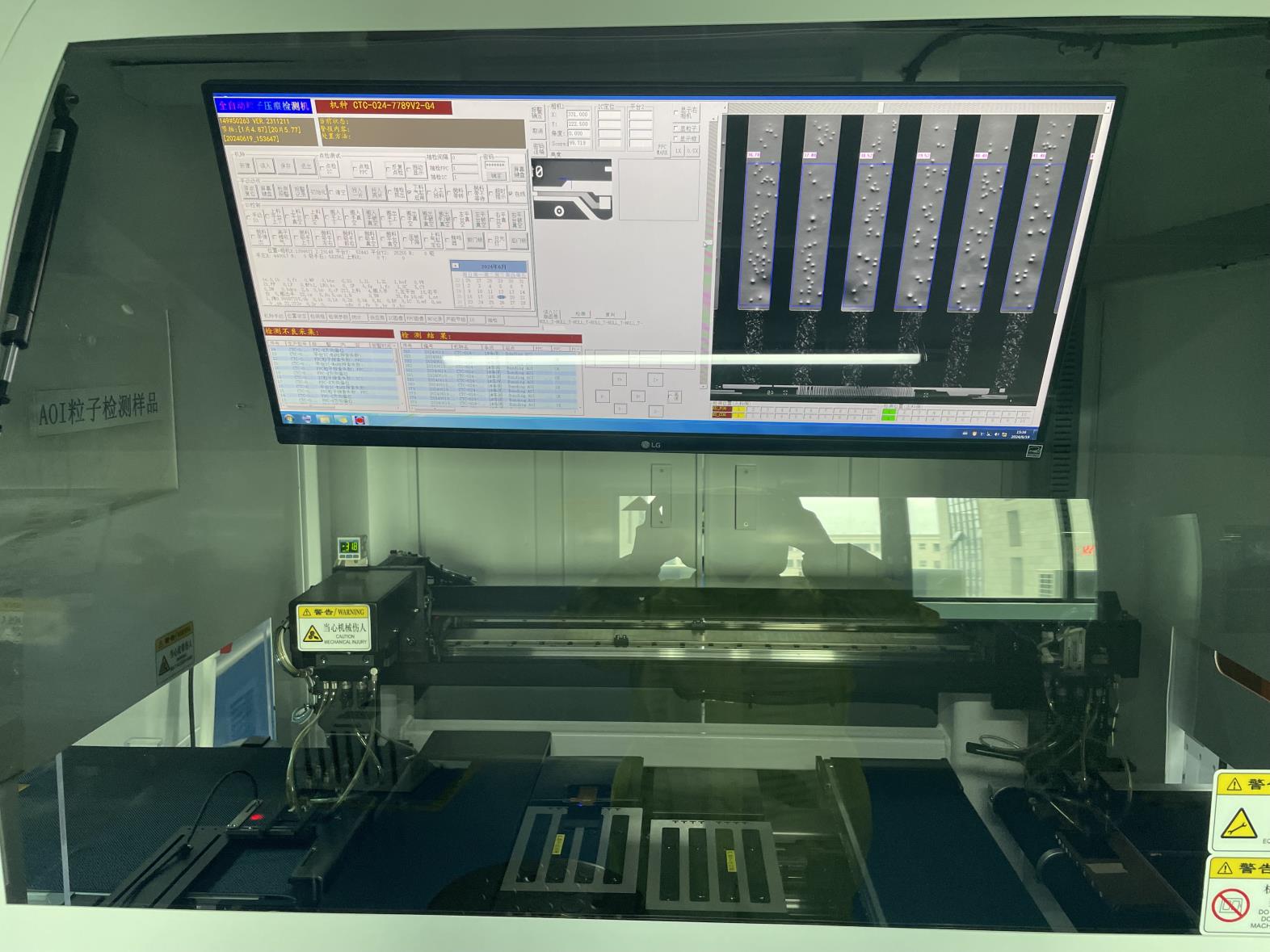

Unsere AOI-Inspektionsgeräte sind so konzipiert, dass sie manuelle Inspektionen ersetzen, die Auswirkungen menschlicher Ermüdung beseitigen und die Wahrscheinlichkeit menschlicher Fehler erheblich reduzieren. Nach der AOI-Prüfung weisen unsere Produkte eine Funktionsausfallrate von weniger als 300 PPM auf, was die Produktqualität erheblich verbessert. Unsere Systeme können verschiedene Defekte genau erkennen, darunter Punktdefekte (helle oder dunkle Flecken) mit einer Größe von 5 μm, Fremdkörperdefekte mit einer Größe von 50 μm, 2 % Erkennungsgenauigkeit für Mura-Defekte auf Graubildschirmen und ±0,0002 Genauigkeit für Farbdefekte mit geringem Kontrast. Sie können auch eine Vielzahl anderer Defekte erkennen, wie z. B. Liniendefekte, hinterleuchtete Fremdkörper, Anzeigeanomalien, Lichtaustritt an den Rändern, Farbtemperaturabweichungen und verschiedene Arten von Mura-Defekten.
Unsere AOI-Inspektionsgeräte sind so konzipiert, dass sie manuelle Inspektionen ersetzen, die Auswirkungen menschlicher Ermüdung beseitigen und die Wahrscheinlichkeit menschlicher Fehler erheblich reduzieren. Nach der AOI-Prüfung weisen unsere Produkte eine Funktionsausfallrate von weniger als 300 PPM auf, was die Produktqualität erheblich verbessert. Unsere Systeme können verschiedene Defekte genau erkennen, darunter Punktdefekte (helle oder dunkle Flecken) mit einer Größe von 5 μm, Fremdkörperdefekte mit einer Größe von 50 μm, 2 % Erkennungsgenauigkeit für Mura-Defekte auf Graubildschirmen und ±0,0002 Genauigkeit für Farbdefekte mit geringem Kontrast. Sie können auch eine Vielzahl anderer Defekte erkennen, wie z. B. Liniendefekte, hinterleuchtete Fremdkörper, Anzeigeanomalien, Lichtaustritt an den Rändern, Farbtemperaturabweichungen und verschiedene Arten von Mura-Defekten.

Unser umfassender Inspektionsprozess
Bei BROWNLH ist die Qualitätskontrolle ein entscheidender Teil des Produktionsprozesses. Um sicherzustellen, dass jedes TFT-Displaymodul den höchsten Qualitätsstandards entspricht, haben wir einen umfassenden und strengen Inspektionsprozess implementiert. Hier sind die acht wichtigsten Inspektionsmethoden, die wir während des Produktionsprozesses durchführen:
Unser Zuverlässigkeitstestprozess
Wir bei unserem Unternehmen legen Wert darauf, unseren Kunden die beste Leistung und Zuverlässigkeit zu bieten. Deshalb unterziehen wir alle unsere Produkte einem umfassenden Testverfahren, bevor wir sie ausliefern. Dies umfasst die oben genannten verschiedenen Methoden und Schlüsselpunkte sowie alle zusätzlichen Qualitätsprüfungsverfahren, die für bestimmte Displays erforderlich sein können. Mit unseren strengen Testmaßnahmen können wir sicherstellen, dass unsere Kunden von uns qualitativ hochwertige und zuverlässige Produkte erhalten.
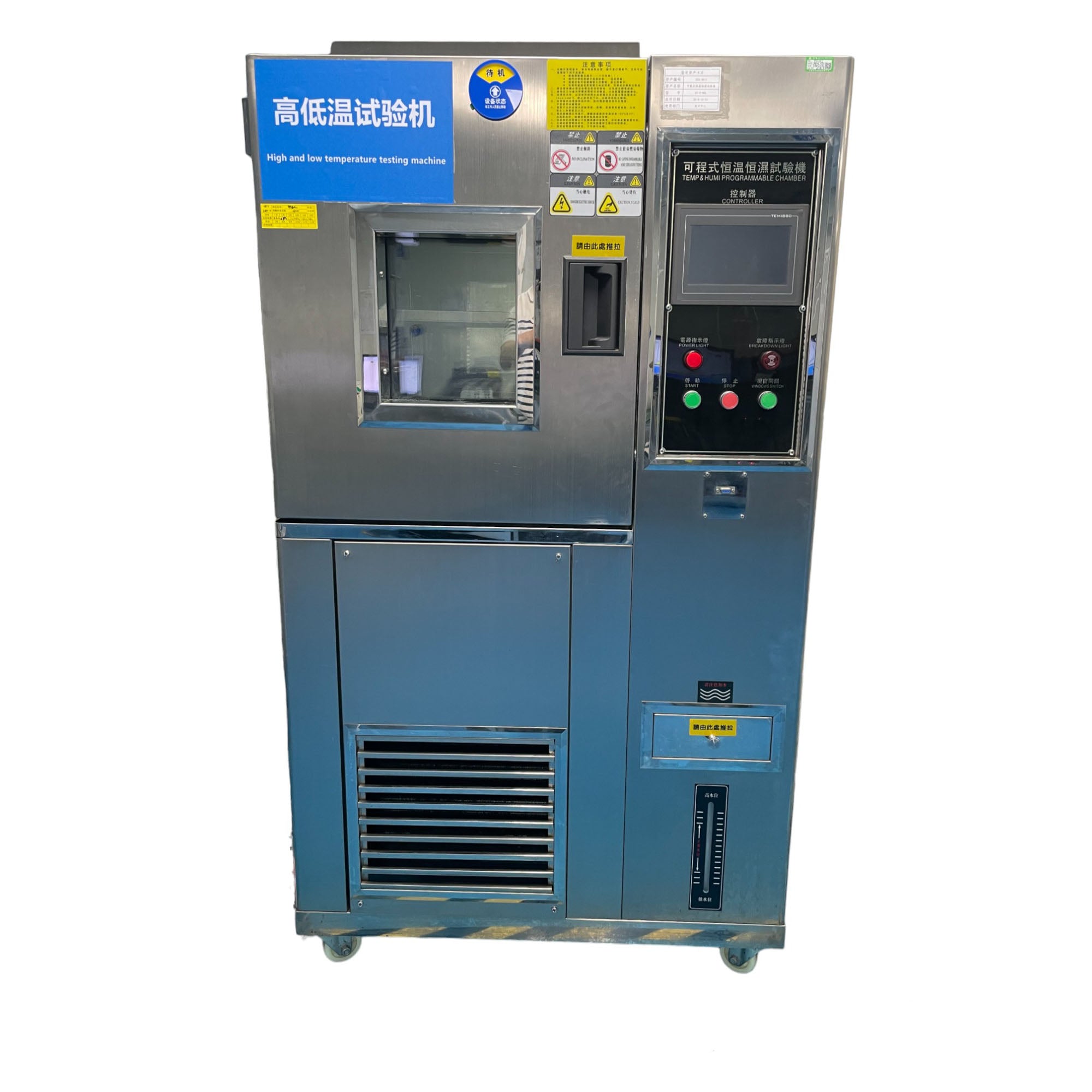
- Testbedingungen für die Lagerung bei hohen Temperaturen: 85 °C ± 3 °C für 1000 Stunden, bei einer relativen Luftfeuchtigkeit von nicht mehr als 45 %.
- Nach der Lagerzeit wird das Produkt für 2 Stunden bei 25 °C wiederhergestellt.
- Um sicherzustellen, dass das Produkt weiterhin ordnungsgemäß funktioniert, wird eine Prüfung außerhalb des Betriebs durchgeführt.
- Dieser Test entspricht den folgenden Spezifikationen: IEC60068-2-2 und GB2423.2.
- Der Test wird mit einem programmierbaren Hochtemperaturtester durchgeführt.
- Testbedingungen für die Lagerung bei hohen Temperaturen: 85 °C ± 3 °C für 1000 Stunden, bei einer relativen Luftfeuchtigkeit von nicht mehr als 45 %.
- Nach der Lagerzeit wird das Produkt für 2 Stunden bei 25 °C wiederhergestellt.
- Um sicherzustellen, dass das Produkt weiterhin ordnungsgemäß funktioniert, wird eine Prüfung außerhalb des Betriebs durchgeführt.
- Dieser Test entspricht den folgenden Spezifikationen: IEC60068-2-2 und GB2423.2.
- Der Test wird mit einem programmierbaren Hochtemperaturtester durchgeführt.
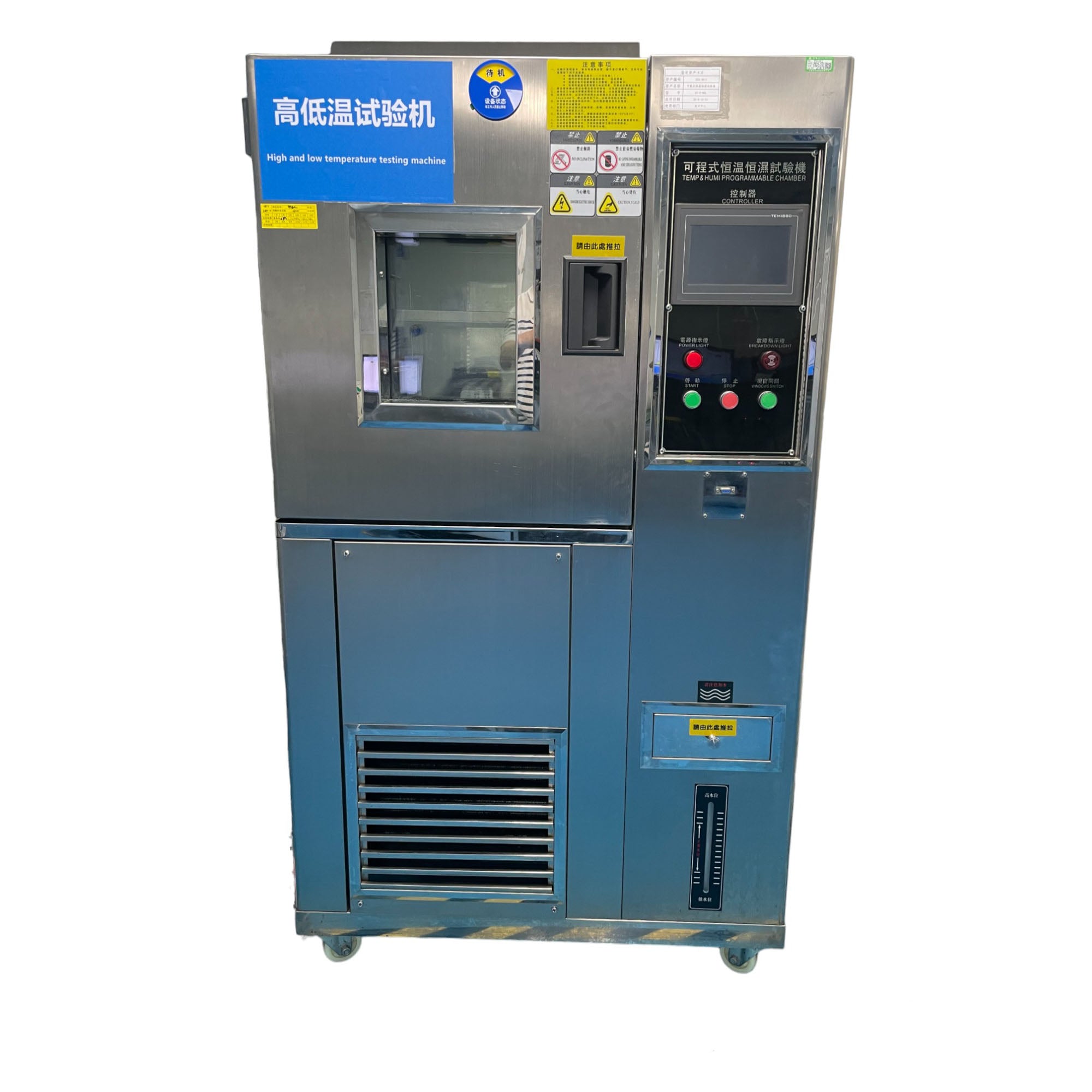
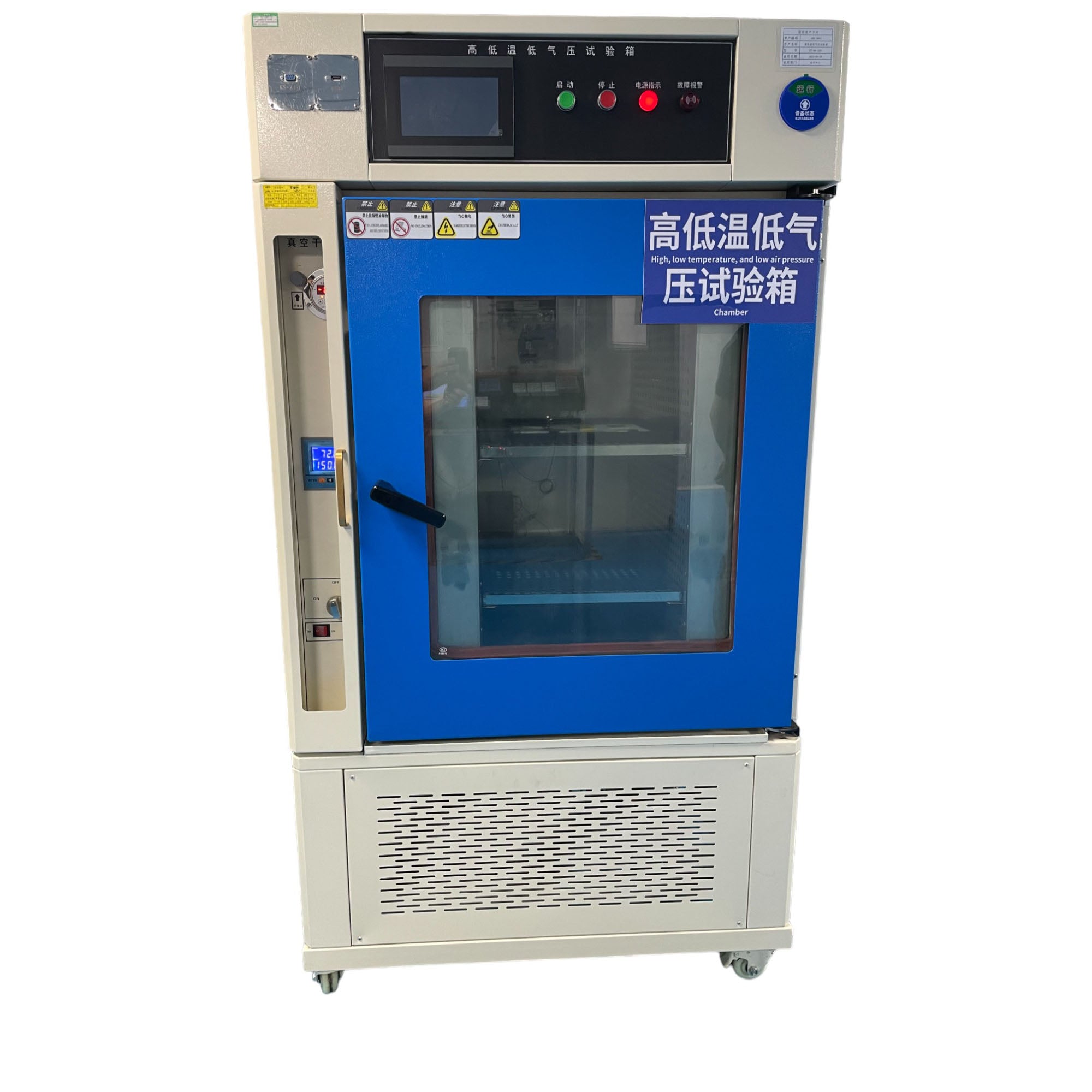
- Testbedingungen für die Lagerung bei niedrigen Temperaturen: -40 °C ± 3 °C für 1000 Stunden.
- Nach der Lagerzeit wird das Produkt für 2 Stunden bei 25 °C wiederhergestellt.
- Es wird eine Außerbetriebnahmeprüfung durchgeführt.
- Im Temperaturbereich von -40 °C bis -30 °C ist die Betriebsleistung nicht garantiert.
- Sofern jedoch keine Funktionsbeeinträchtigungen vorliegen, gilt die Prüfung als in Ordnung.
- Dieser Test entspricht den folgenden Spezifikationen: IEC60068-2-1 und GB2423.1.
- Der Test wird mit den erforderlichen Geräten und Werkzeugen durchgeführt.
- Testbedingungen für die Lagerung bei niedrigen Temperaturen: -40 °C ± 3 °C für 1000 Stunden.
- Nach der Lagerzeit wird das Produkt für 2 Stunden bei 25 °C wiederhergestellt.
- Es wird eine Außerbetriebnahmeprüfung durchgeführt.
- Im Temperaturbereich von -40 °C bis -30 °C ist die Betriebsleistung nicht garantiert.
- Sofern jedoch keine Funktionsbeeinträchtigungen vorliegen, gilt die Prüfung als in Ordnung.
- Dieser Test entspricht den folgenden Spezifikationen: IEC60068-2-1 und GB2423.1.
- Der Test wird mit den erforderlichen Geräten und Werkzeugen durchgeführt.
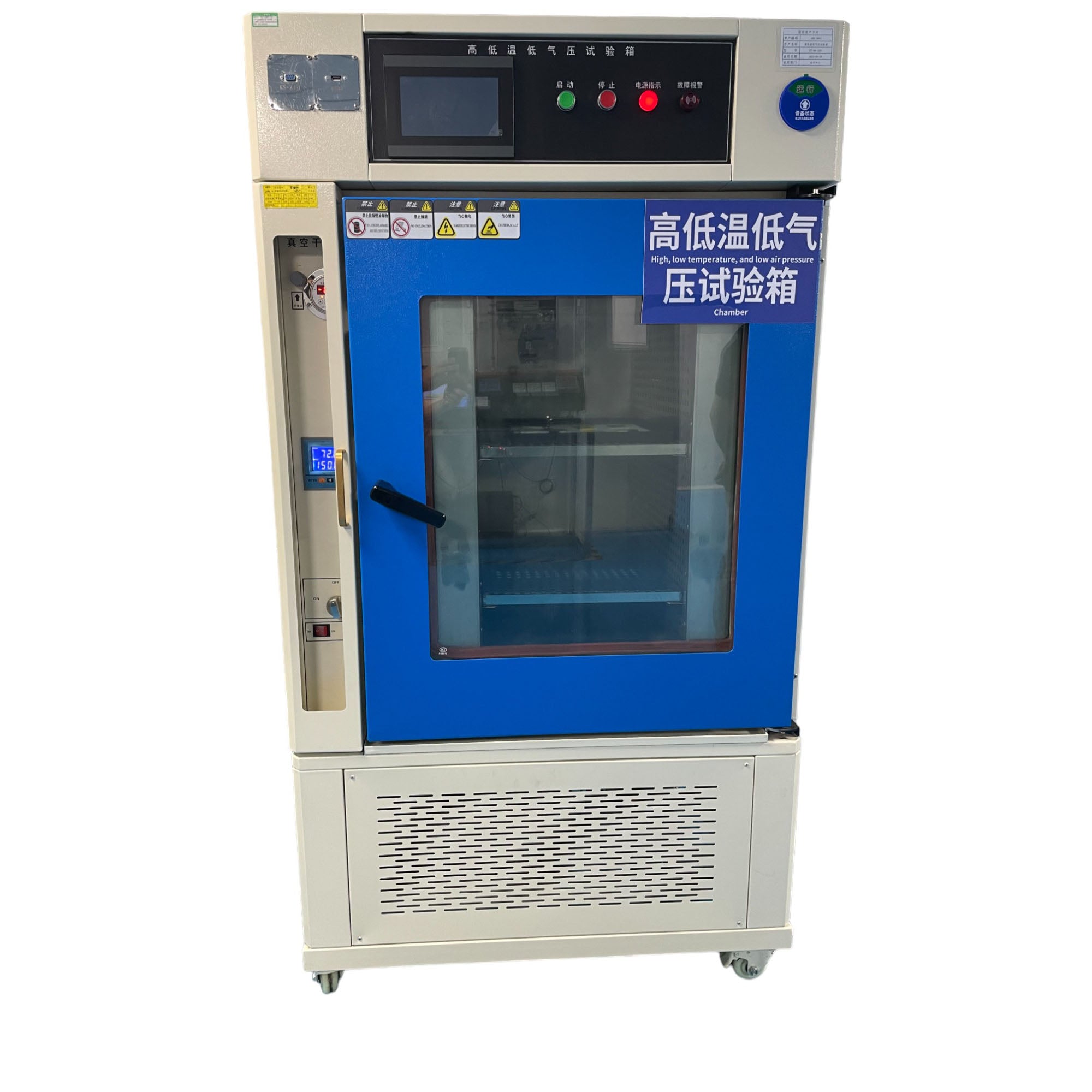
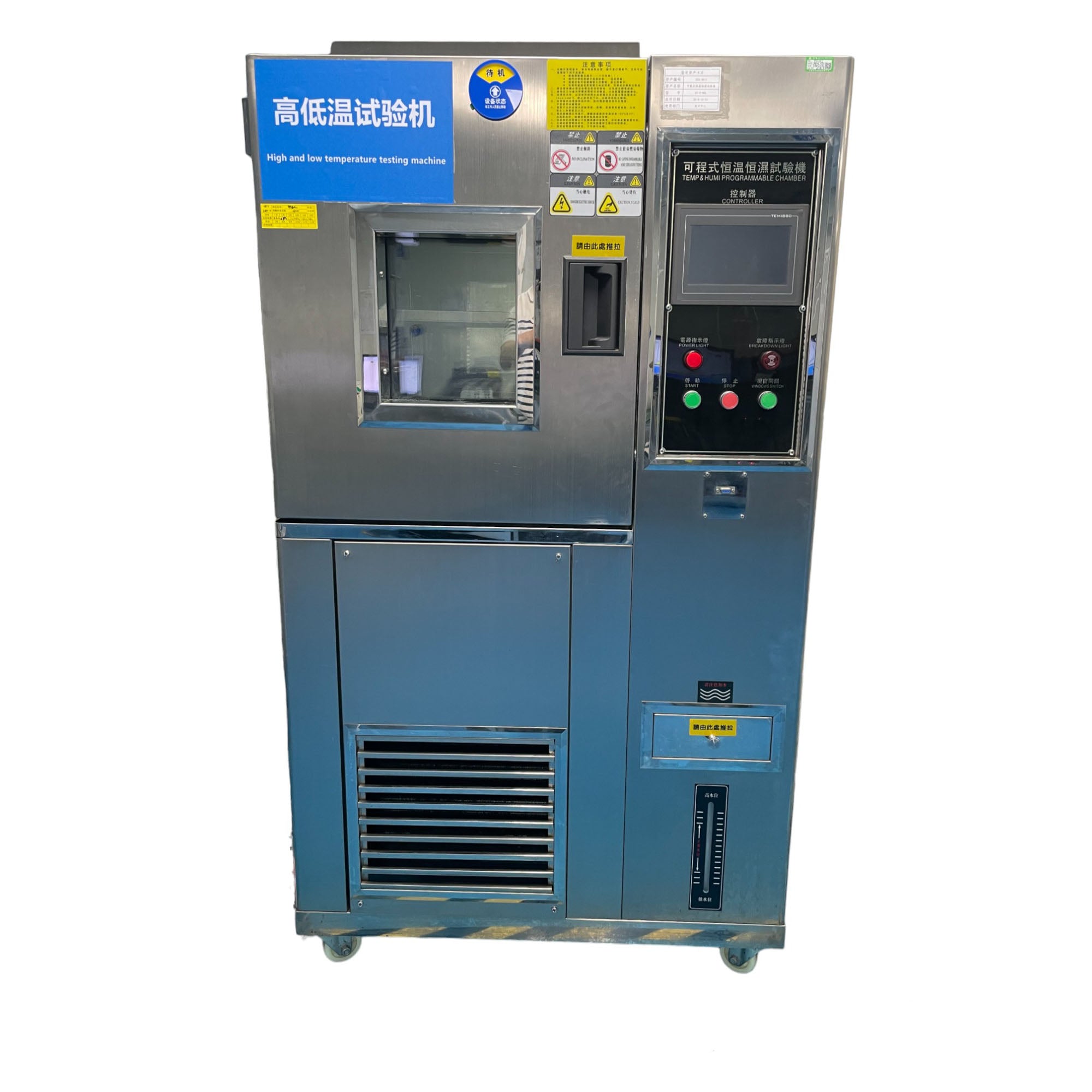
- Testbedingungen für den Hochtemperaturbetrieb: 85 °C ± 3 °C für 1000 Stunden.
- Nach der Betriebszeit wird das Produkt für 2 Stunden bei 25 °C wiederhergestellt.
- Um sicherzustellen, dass das Produkt weiterhin ordnungsgemäß funktioniert, wird eine Funktionsprüfung durchgeführt.
- Dieser Test entspricht den folgenden Spezifikationen: IEC60068-2-2 und GB2423.2.
- Der Test wird mit einem programmierbaren Hochtemperaturtester durchgeführt.
- Testbedingungen für den Hochtemperaturbetrieb: 85 °C ± 3 °C für 1000 Stunden.
- Nach der Betriebszeit wird das Produkt für 2 Stunden bei 25 °C wiederhergestellt.
- Um sicherzustellen, dass das Produkt weiterhin ordnungsgemäß funktioniert, wird eine Funktionsprüfung durchgeführt.
- Dieser Test entspricht den folgenden Spezifikationen: IEC60068-2-2 und GB2423.2.
- Der Test wird mit einem programmierbaren Hochtemperaturtester durchgeführt.
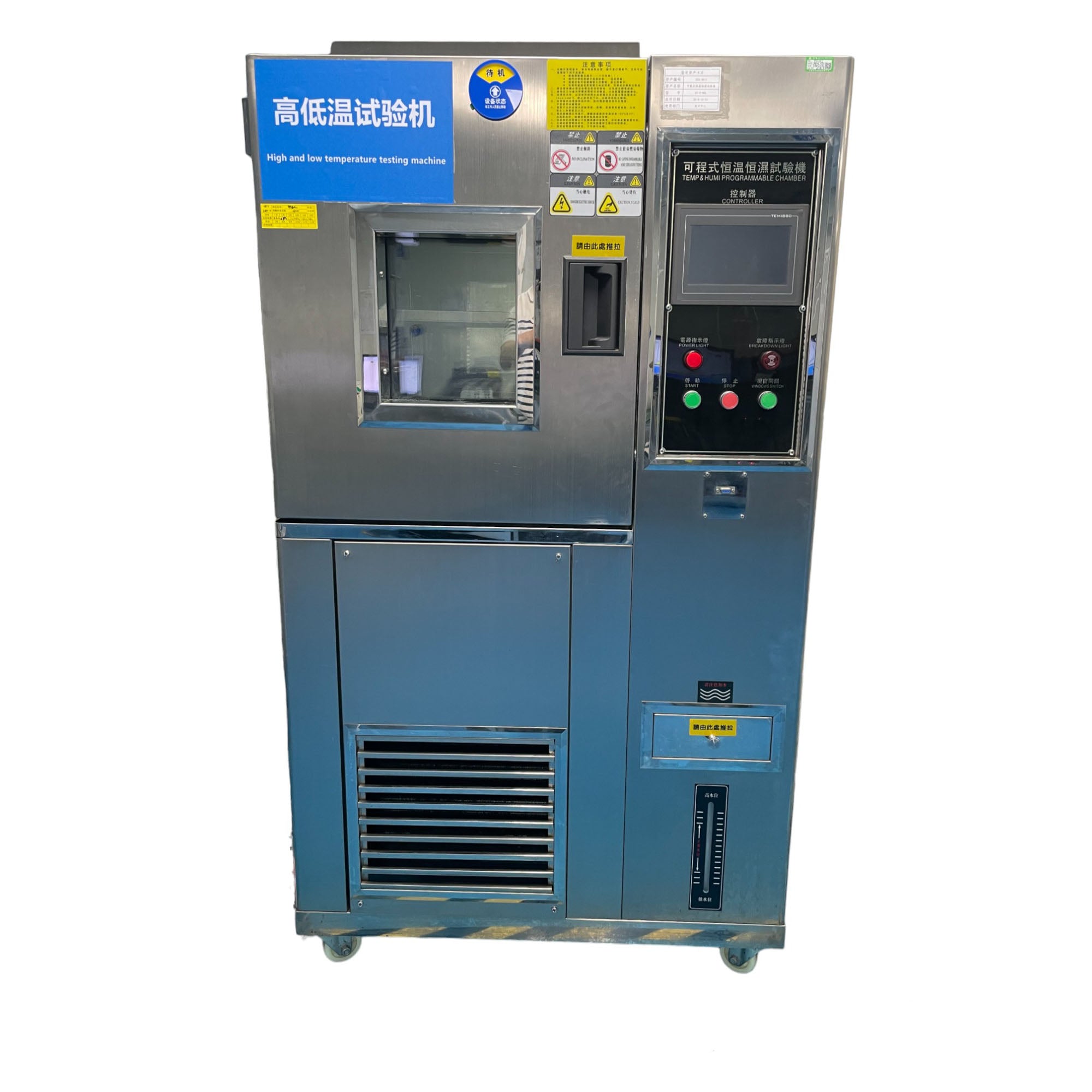
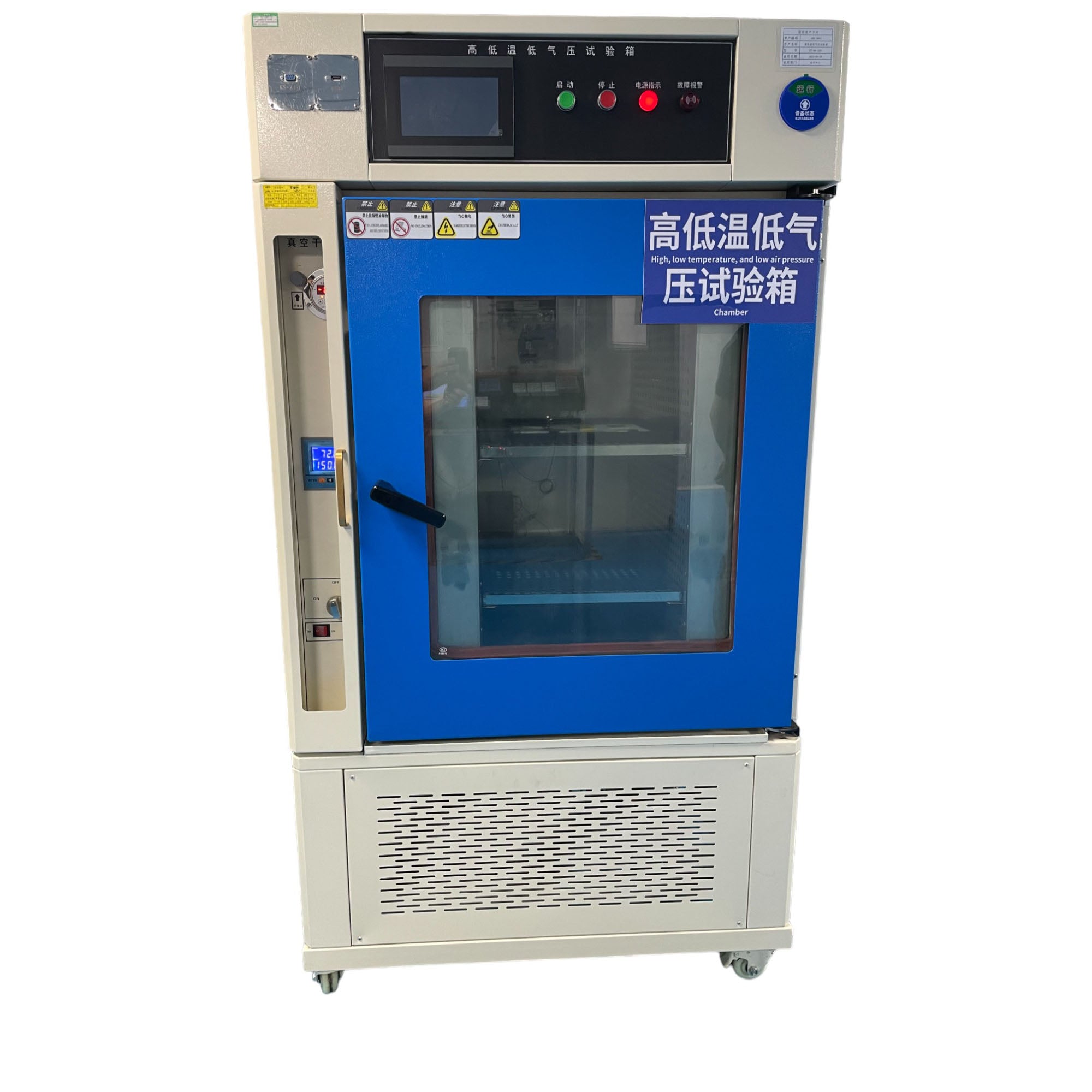
- Testbedingungen für den Betrieb bei niedrigen Temperaturen: -30 °C ± 3 °C für 1000 Stunden.
- Nach der Betriebszeit wird das Produkt für 2 Stunden bei 25 °C wiederhergestellt.
- Um sicherzustellen, dass das Produkt weiterhin ordnungsgemäß funktioniert, wird eine Funktionsprüfung durchgeführt.
- Dieser Test entspricht den folgenden Spezifikationen: IEC60068-2-1 und GB2423.1.
- Der Test wird mit einem programmierbaren Niedertemperaturtester durchgeführt.
- Testbedingungen für den Betrieb bei niedrigen Temperaturen: -30 °C ± 3 °C für 1000 Stunden.
- Nach der Betriebszeit wird das Produkt für 2 Stunden bei 25 °C wiederhergestellt.
- Um sicherzustellen, dass das Produkt weiterhin ordnungsgemäß funktioniert, wird eine Funktionsprüfung durchgeführt.
- Dieser Test entspricht den folgenden Spezifikationen: IEC60068-2-1 und GB2423.1.
- Der Test wird mit einem programmierbaren Niedertemperaturtester durchgeführt.
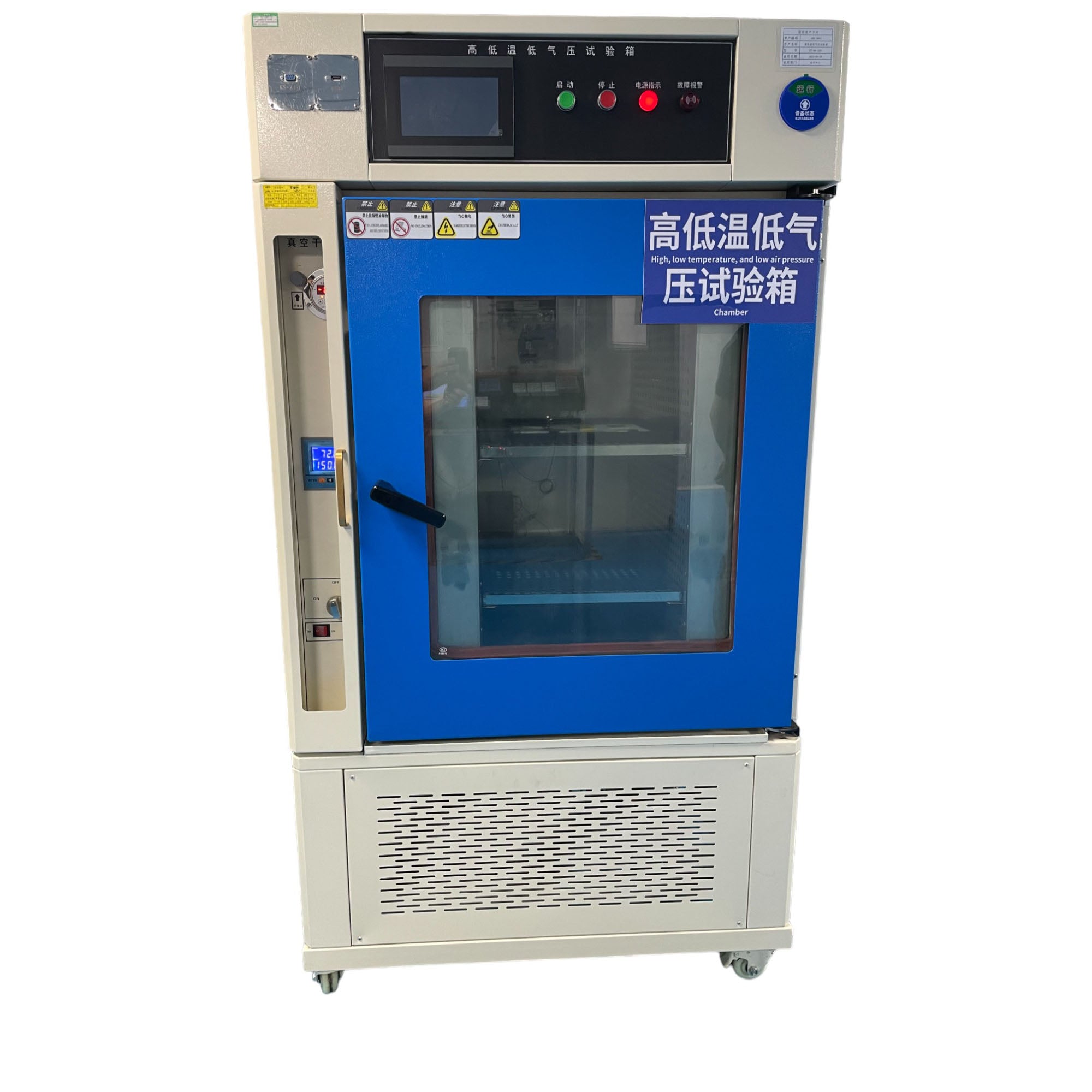
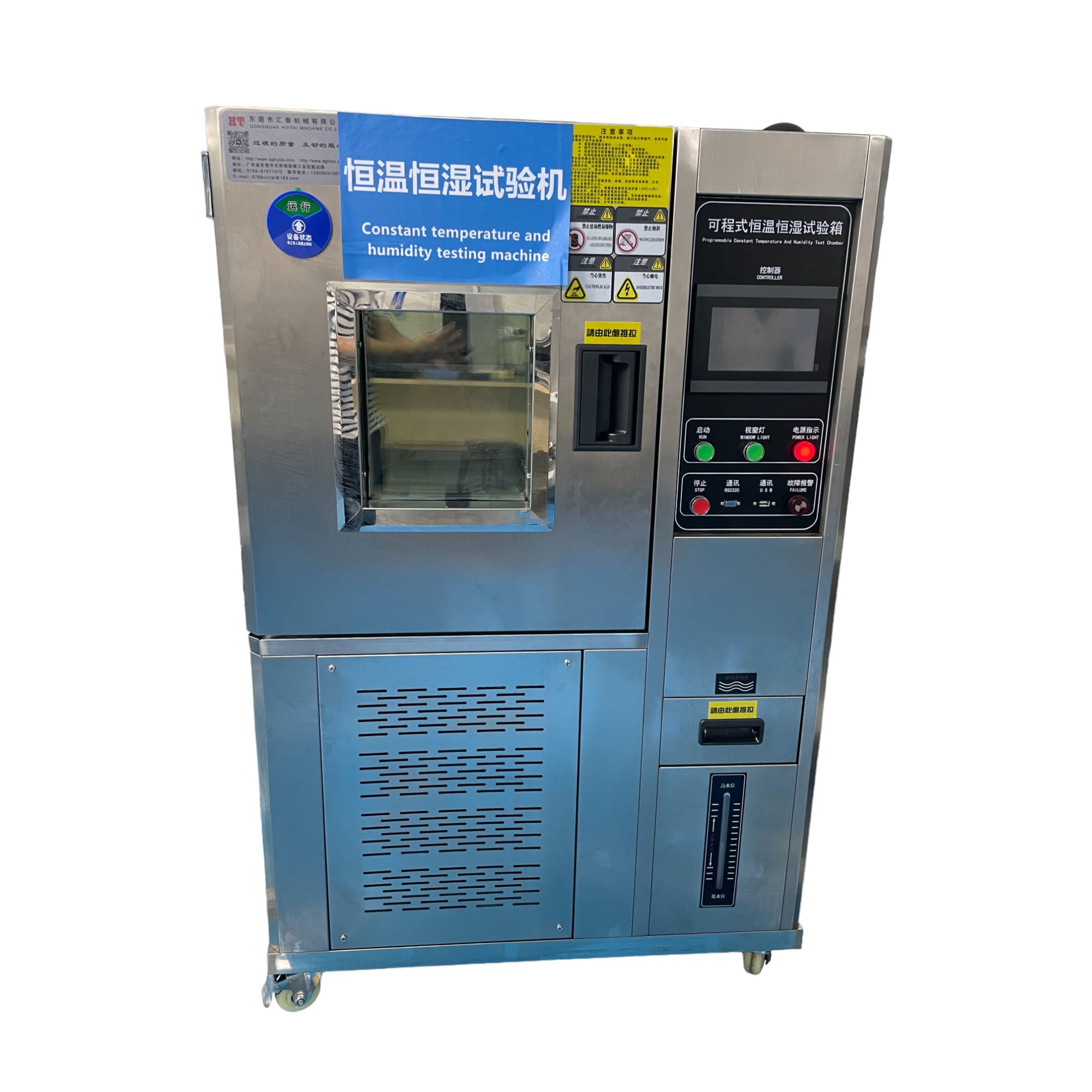
- Testbedingungen für den Betrieb bei hohen Temperaturen und hoher Luftfeuchtigkeit: 85 °C ± 2 °C und 85 ± 2 % relative Luftfeuchtigkeit für 1000 Stunden.
- Nach der Betriebszeit wird das Produkt für 2 Stunden bei Raumtemperatur belassen, bevor es auf Funktionsfähigkeit geprüft wird.
- Dieser Test entspricht den folgenden Spezifikationen: IEC60068-2-78 und GB/T2423.3.
- Der Test wird mit einem Konstanttemperatur- und Feuchtigkeitstester durchgeführt.
- Testbedingungen für den Betrieb bei hohen Temperaturen und hoher Luftfeuchtigkeit: 85 °C ± 2 °C und 85 ± 2 % relative Luftfeuchtigkeit für 1000 Stunden.
- Nach der Betriebszeit wird das Produkt für 2 Stunden bei Raumtemperatur belassen, bevor es auf Funktionsfähigkeit geprüft wird.
- Dieser Test entspricht den folgenden Spezifikationen: IEC60068-2-78 und GB/T2423.3.
- Der Test wird mit einem Konstanttemperatur- und Feuchtigkeitstester durchgeführt.
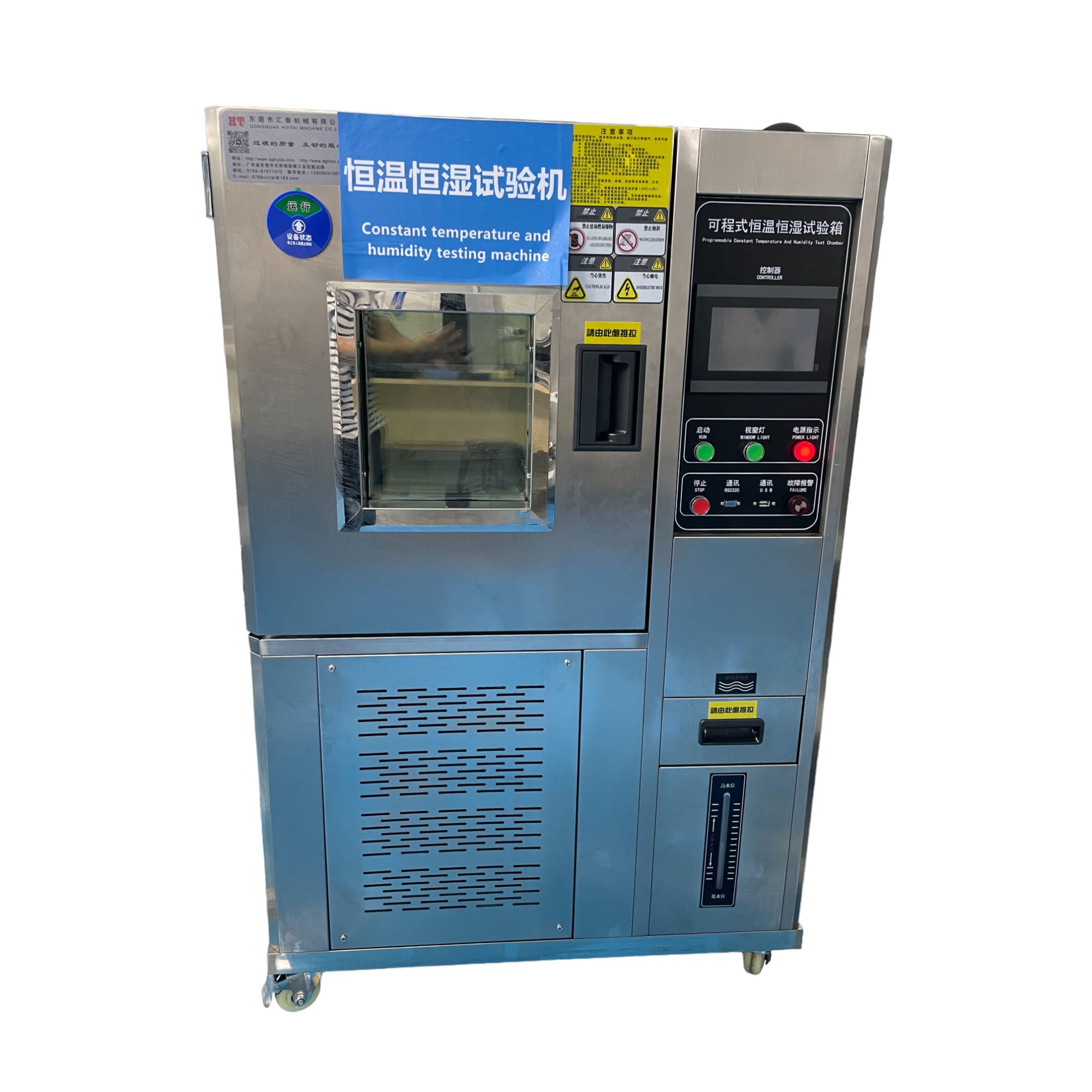
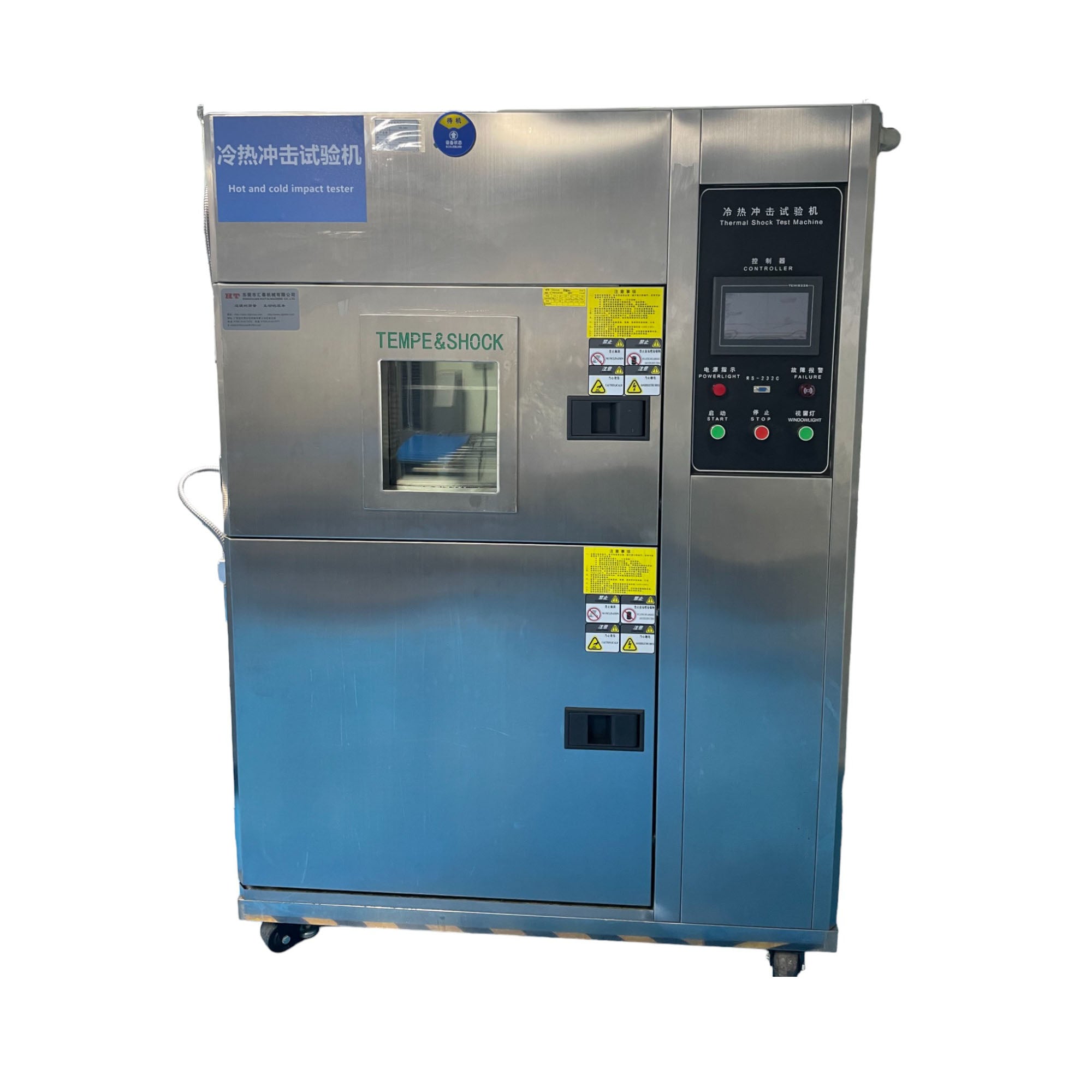
- Bedingungen für den Thermoschocktest: -40 °C für 30 Minuten, dann Wechsel auf +85 °C für 5 Minuten und schließlich wieder zurück auf -40 °C für weitere 30 Minuten, insgesamt 1000 Zyklen.
- Das Produkt ist während dieses Tests nicht betriebsbereit und beginnt mit einer kalten Temperatur und endet mit einer hohen Temperatur.
- Dieser Test entspricht den folgenden Spezifikationen: IEC60068-2-14 und GB2423.22.
- Der Test wird mit einem Thermoschocktester durchgeführt.
- Bedingungen für den Thermoschocktest: -40 °C für 30 Minuten, dann Wechsel auf +85 °C für 5 Minuten und schließlich wieder zurück auf -40 °C für weitere 30 Minuten, insgesamt 1000 Zyklen.
- Das Produkt ist während dieses Tests nicht betriebsbereit und beginnt mit einer kalten Temperatur und endet mit einer hohen Temperatur.
- Dieser Test entspricht den folgenden Spezifikationen: IEC60068-2-14 und GB2423.22.
- Der Test wird mit einem Thermoschocktester durchgeführt.
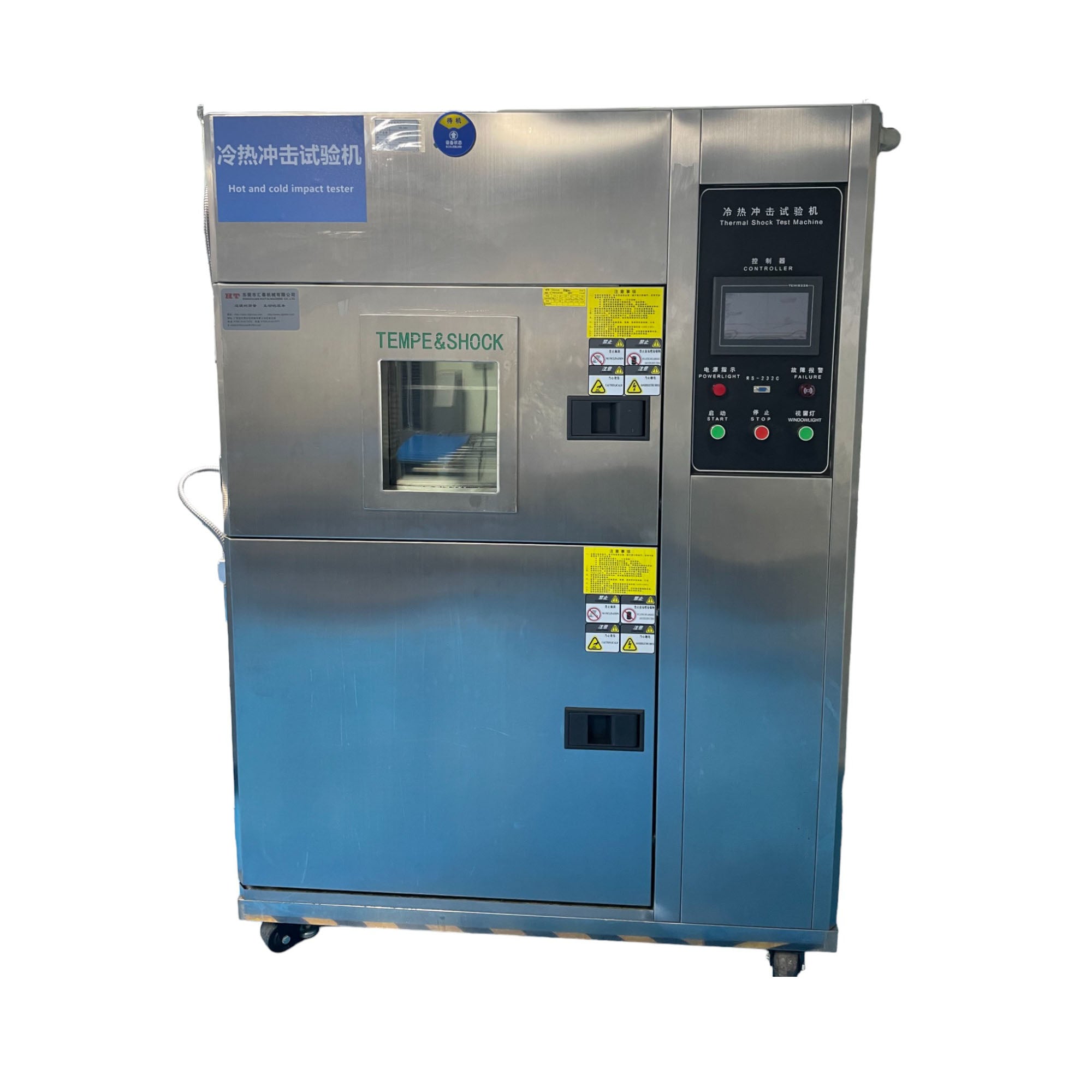
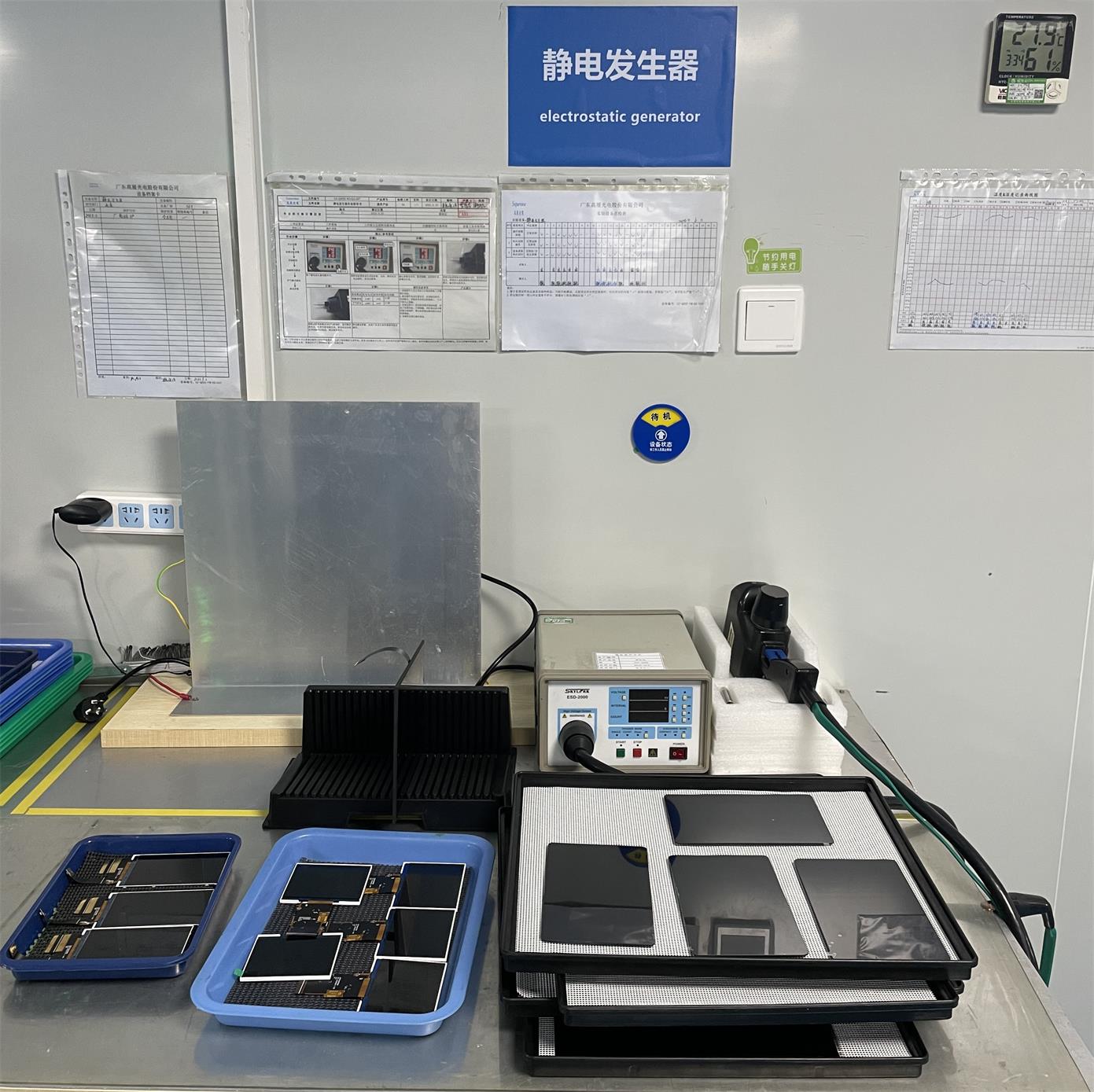
- ESD-Testbedingungen (elektrostatische Entladung): C=150pF, R=330Ω, 5-Punkt-/Panel-Oberflächenkontaktentladung: ± 8 kV für 5-mal (Klasse B) und Luftentladung: ± 15 kV für 5-mal (Klasse B).
- Dieser Test entspricht den folgenden Spezifikationen: IEC61000-4-2 und GB/T17626.2.
- Der Test wird mit einem Generator für elektrostatische Entladung durchgeführt.
- ESD-Testbedingungen (elektrostatische Entladung): C=150pF, R=330Ω, 5-Punkt-/Panel-Oberflächenkontaktentladung: ± 8 kV für 5-mal (Klasse B) und Luftentladung: ± 15 kV für 5-mal (Klasse B).
- Dieser Test entspricht den folgenden Spezifikationen: IEC61000-4-2 und GB/T17626.2.
- Der Test wird mit einem Generator für elektrostatische Entladung durchgeführt.
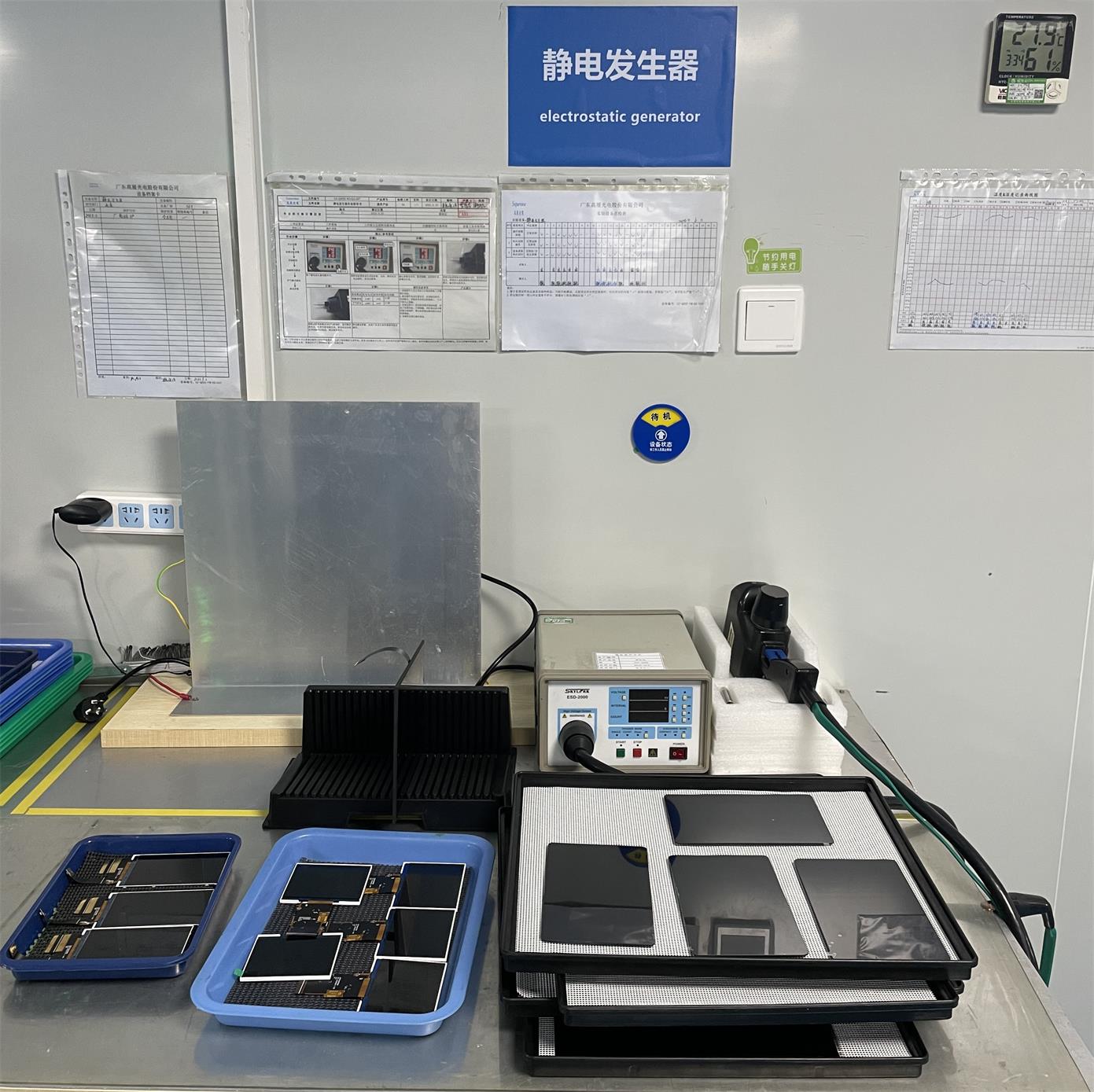
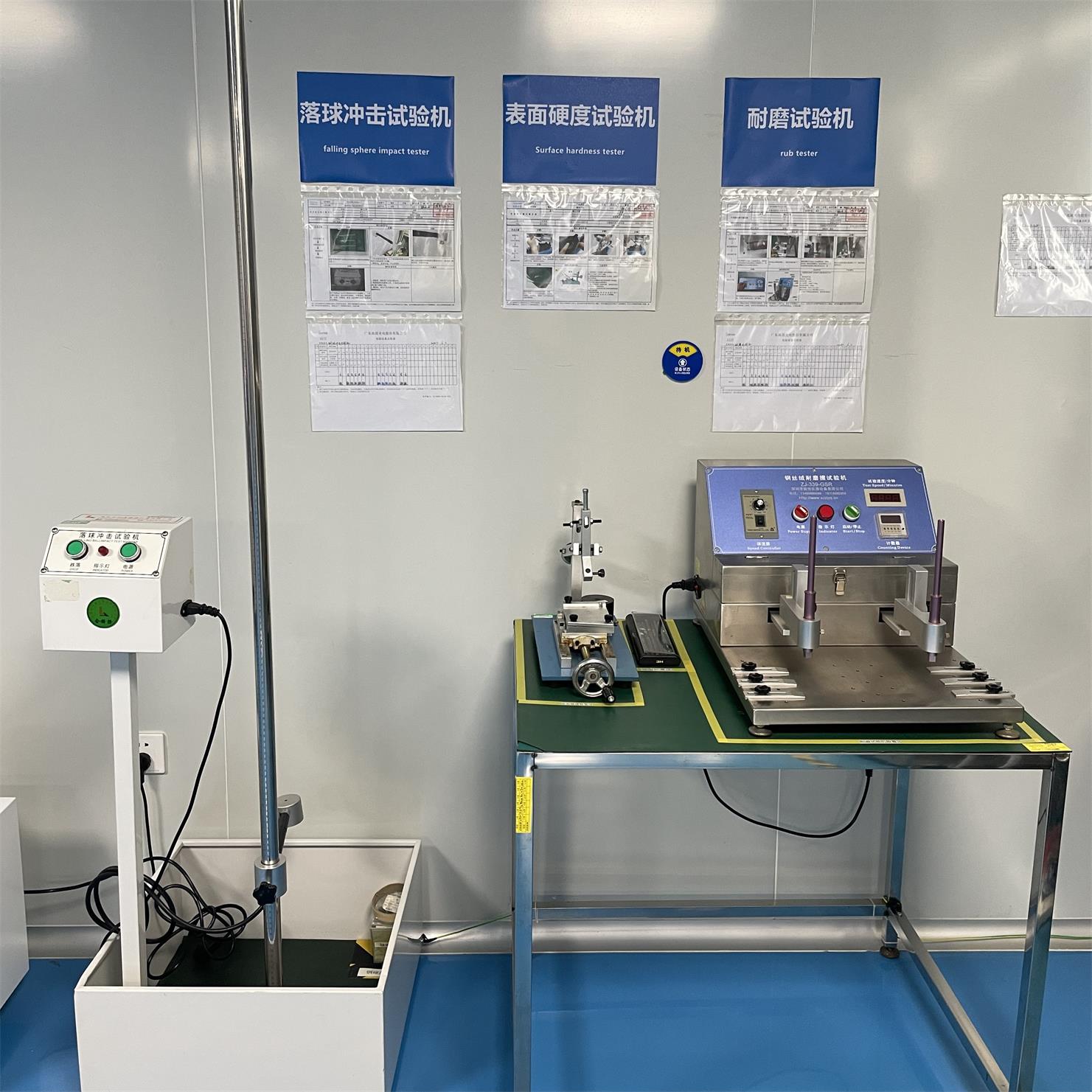
- Bedingungen für den mechanischen Stoßtest: Halbe Sinuswelle, 100 G für 6 ms, ± X, ± Y, ± Z dreimal in jede Richtung.
- Das Produkt ist während dieses Tests ausgeschaltet.
- Dieser Test entspricht den folgenden Spezifikationen: IEC 60068-2-27-2008 und GB/T 2423.5.
- Der Test wird mit einem Aufprallprüfgerät durchgeführt.
- Bedingungen für den mechanischen Stoßtest: Halbe Sinuswelle, 100 G für 6 ms, ± X, ± Y, ± Z dreimal in jede Richtung.
- Das Produkt ist während dieses Tests ausgeschaltet.
- Dieser Test entspricht den folgenden Spezifikationen: IEC 60068-2-27-2008 und GB/T 2423.5.
- Der Test wird mit einem Aufprallprüfgerät durchgeführt.
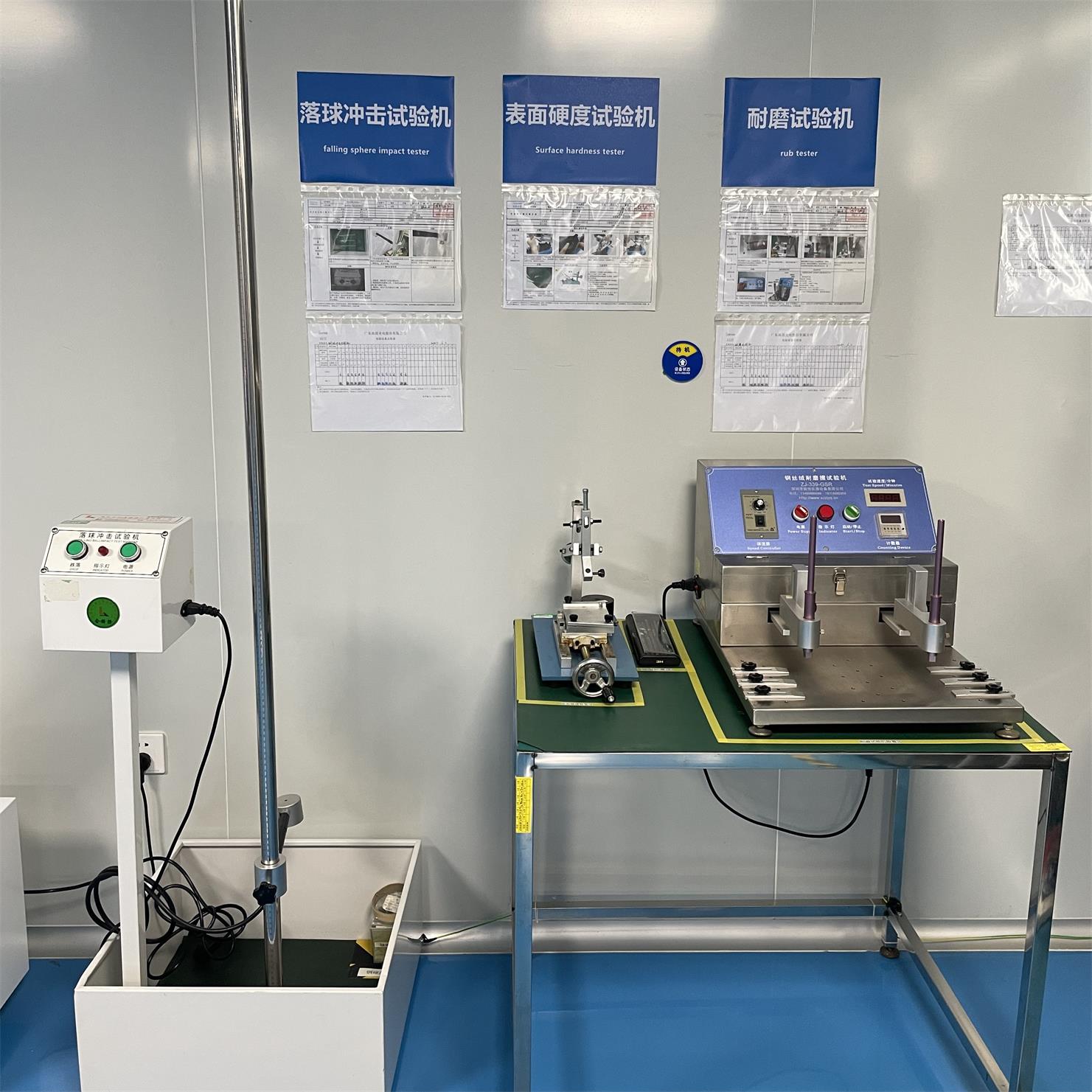
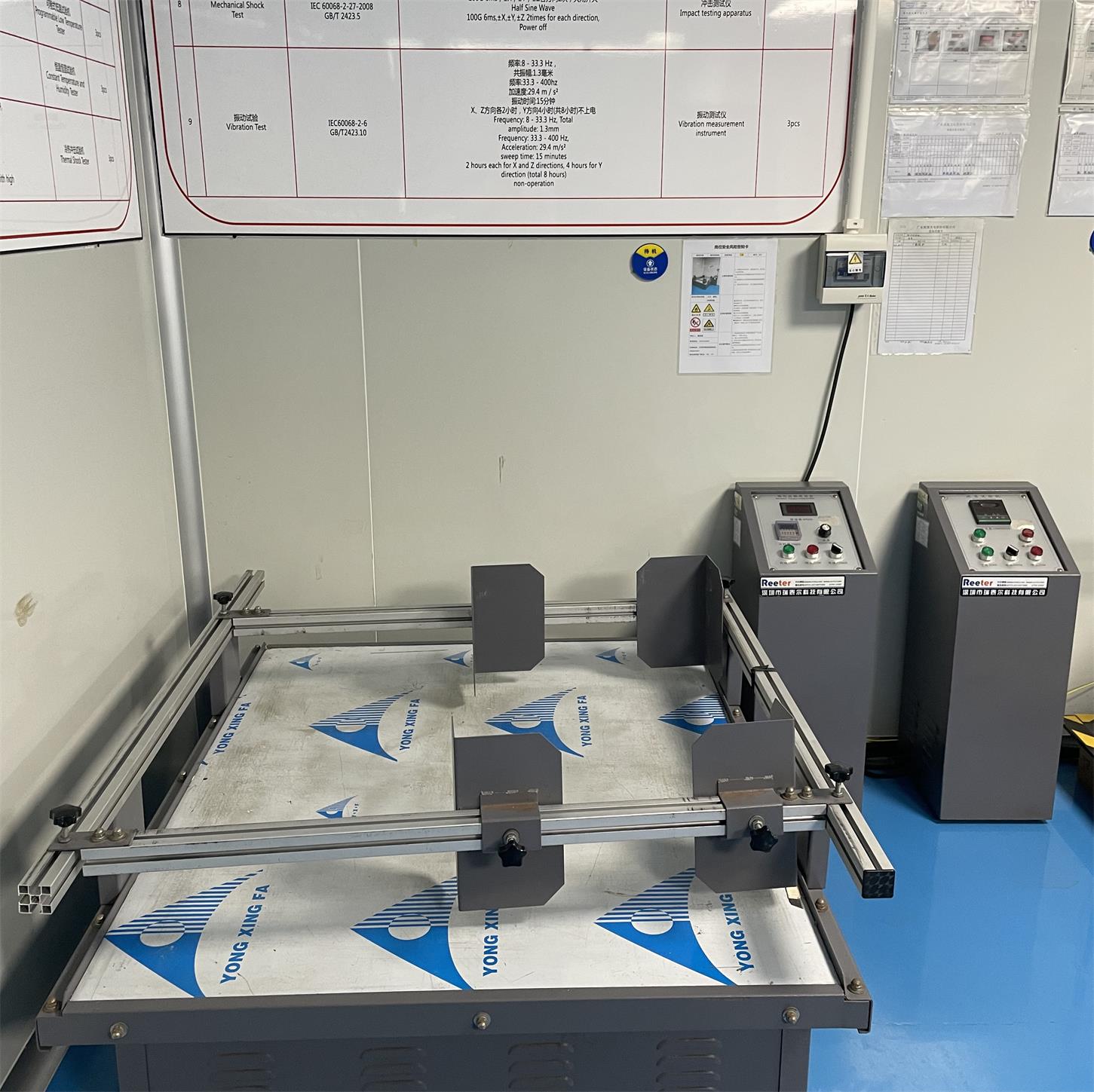
- Vibrationstestbedingungen: Frequenz: 8 – 33,3 Hz, Gesamtamplitude: 1,3 mm, Beschleunigung: 29,4 m/s², Sweep-Zeit: 15 Minuten.
- Der Test wird jeweils 2 Stunden in X- und Z-Richtung und 4 Stunden in Y-Richtung durchgeführt, also insgesamt 8 Stunden.
- Während dieses Tests ist das Produkt nicht betriebsbereit.
- Dieser Test entspricht den folgenden Spezifikationen: IEC60068-2-6 und GB/T2423.10.
- Der Test wird mit einem Vibrationsmessgerät durchgeführt.
- Vibrationstestbedingungen: Frequenz: 8 – 33,3 Hz, Gesamtamplitude: 1,3 mm, Beschleunigung: 29,4 m/s², Sweep-Zeit: 15 Minuten.
- Der Test wird jeweils 2 Stunden in X- und Z-Richtung und 4 Stunden in Y-Richtung durchgeführt, also insgesamt 8 Stunden.
- Während dieses Tests ist das Produkt nicht betriebsbereit.
- Dieser Test entspricht den folgenden Spezifikationen: IEC60068-2-6 und GB/T2423.10.
- Der Test wird mit einem Vibrationsmessgerät durchgeführt.
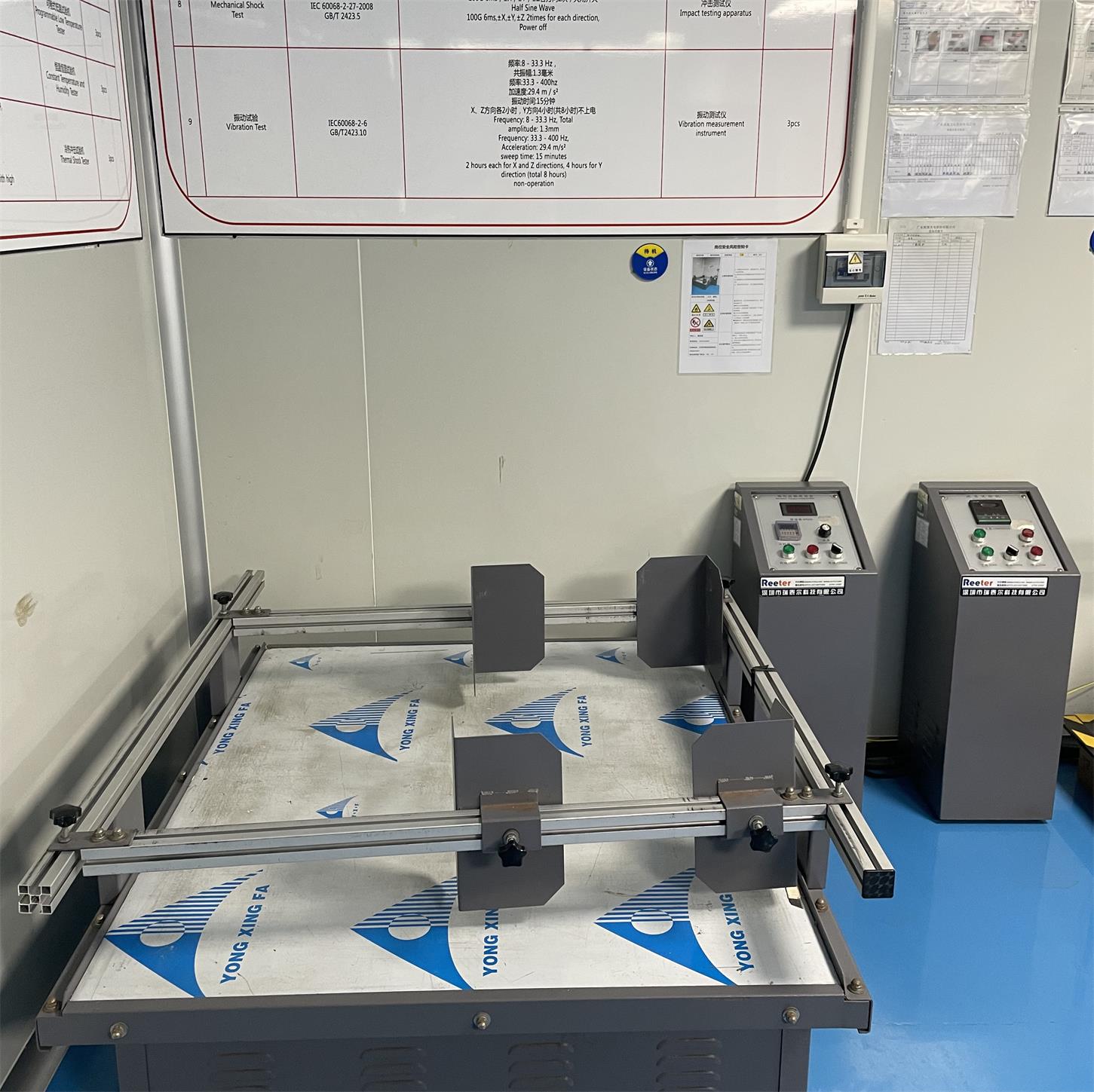
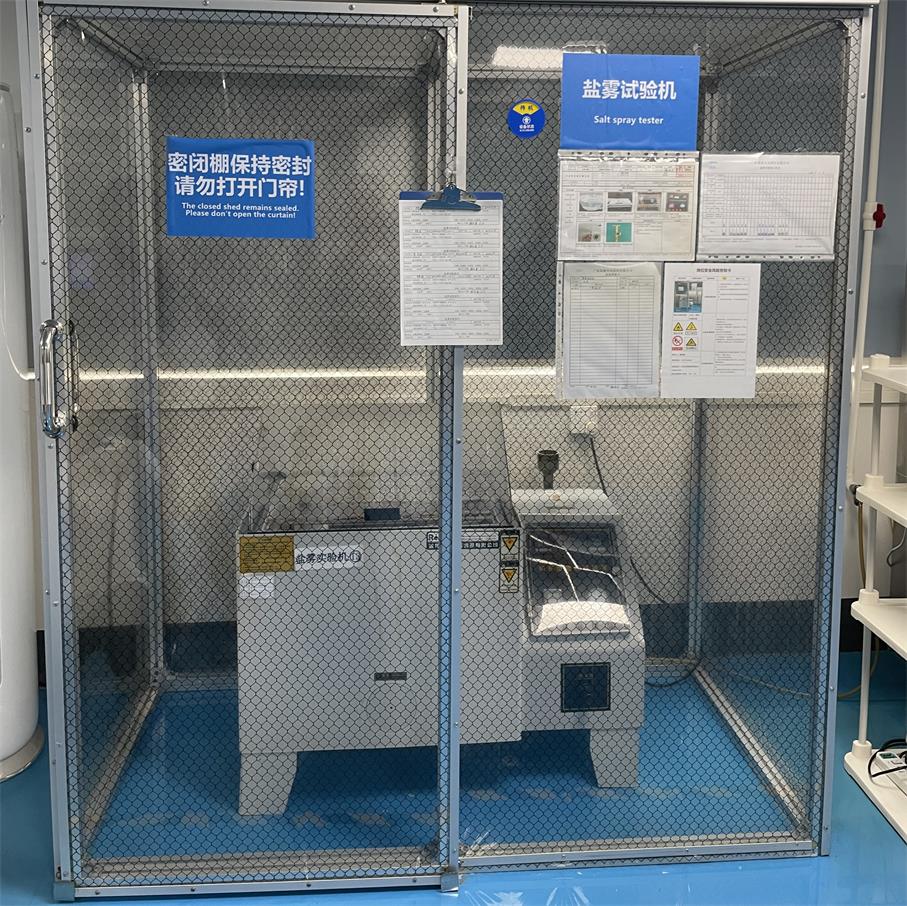
- Bedingungen für den Salzsprühtest: Testtemperatur: 35 °C, spezifisches Gewicht der Salzlösung: 1,020 – 1,040, pH-Wert: 6,5 – 7,2, Natriumchloridgehalt: 5 % ± 1 %, Sprühdauer 24 Stunden.
- Dieser Test entspricht den folgenden Spezifikationen: IEC60068-2-6 und GB/T2423.1.
- Der Test wird mit einem Salzsprühtester durchgeführt.
- Bedingungen für den Salzsprühtest: Testtemperatur: 35 °C, spezifisches Gewicht der Salzlösung: 1,020 – 1,040, pH-Wert: 6,5 – 7,2, Natriumchloridgehalt: 5 % ± 1 %, Sprühdauer 24 Stunden.
- Dieser Test entspricht den folgenden Spezifikationen: IEC60068-2-6 und GB/T2423.1.
- Der Test wird mit einem Salzsprühtester durchgeführt.
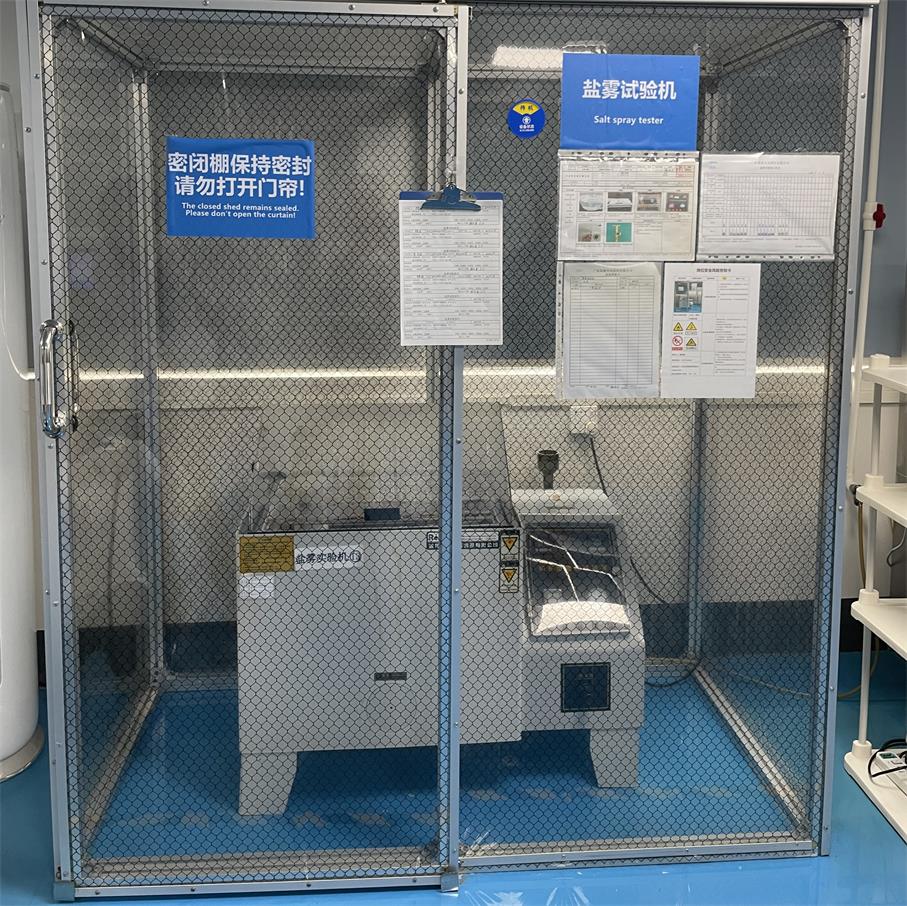