
Die Struktur des TFT-LCD-Displays
- Flüssigkristallanzeige (Anzeige) : Dies ist der Hauptteil des Displays, der für die Bilddarstellung zuständig ist. Die Flüssigkristallanzeige besteht aus zwei Glasplatten, zwischen denen sich eine Schicht Flüssigkristall befindet, die sogenannte Flüssigkristallzelle.
- Polarisationsfilter: Diese Komponenten befinden sich auf beiden Seiten der Flüssigkristallzelle und haben die Aufgabe, das durch die Zelle hindurchtretende Licht zu verarbeiten.
- Farbfilter : Normalerweise auf einer der Glasplatten der versiegelten Flüssigkristallzelle angebracht und wird zur Farbanzeige verwendet.
- Dünnschichttransistor-Array (TFT-Array) : Befindet sich auf der anderen Glasplatte der versiegelten Flüssigkristallzelle und spielt eine aktive Rolle bei der Ansteuerung des Displays.
- Hintergrundbeleuchtung: Die Lichtquelle hinter dem TFT-LCD-Anzeigemodul sorgt für das nötige Licht, damit das sichtbare Bild durch die Flüssigkristallzelle erzeugt werden kann.
- Externe Antriebsschaltkreise: Diese Schaltkreise sind für die Verwaltung der eingehenden Bildsignale zuständig, um das TFT-Array und die Hintergrundbeleuchtung entsprechend anzutreiben.

Der Herstellungsprozess von TFT-LCD-Displays
- Filmbildung : Techniken wie Sputtern (SPT) und chemische Gasphasenabscheidung (CVD) lagern mehrere Schichten auf dem Substrat ab.
- Fotolithografie : Auftragen, Belichten und Entwickeln von Fotolack zur Bildung von Mikrostrukturen.
- Ätzen : Nass- und Trockenätzverfahren formen das Substrat durch Entfernen bestimmter Bereiche.
- Strippen : Nach der Strukturierung werden überschüssige Materialien entfernt, um das Substrat zu reinigen.
Zusätzliche Prozessschritte:
Reinigung: Stellt sicher, dass der Untergrund frei von Verunreinigungen ist.
Markierung und Belichtung: Identifiziert und bereitet die Substratkanten vor.
Automatische optische Inspektion (AOI): Wird zur Defektinspektion verwendet.
Mikroskopische Inspektion und makroskopische Inspektion (Mic/Mac): Detailprüfung.
Prüfung der Filmleistung: Verwendet werden Werkzeuge wie Flächenwiderstandsmessgeräte, Profilometer, Reflektometer/Ellipsometrie und Fourier-Transformations-Infrarotspektroskopie.
Elektrische Prüfung auf Unterbrechung/Kurzschluss (O/S): Überprüft die Stromkreiskontinuität und Kurzschlüsse. Elektrische Prüfung auf Testelementgruppe (TEG): Testet die elektrische Leistung von Elementen.
Elektrische Prüfung des Arrays: Stellt die elektrische Funktionalität des Arrays sicher.
Laserreparatur: Korrigiert alle Defekte entsprechend den Inspektionsergebnissen.
Fotolack-Nacharbeit (PR-Nacharbeit): Passt die Fotolithografie-Schritte bei Bedarf an oder wiederholt sie.
Filmnacharbeitung: Ändert oder perfektioniert bei Bedarf den Filmbildungsprozess.

- OC-Schicht schützt und bereitet die Farbfiltermuster vor.
- RGB-Ebene Bildung durch Beschichtungs-, Belichtungs- und Entwicklungssequenzen.
- BM (Black Matrix)-Schicht verbessert den Kontrast und begrenzt den Lichtverlust.
- PS-Schicht (Photo Spacer) Hält den präzisen Abstand zwischen den Substraten aufrecht, was für die Bildqualität entscheidend ist.
- ITO-Schicht fügt einen transparenten leitfähigen Film für elektrische Leitung und Touch-Funktionalität hinzu.

- Ausrichtung und Orientierung von Polyimid (PI) : Aufbringen und Ausrichten der PI-Schicht zur Ausrichtung der Flüssigkristalle.
- ODF (Optischer Displayfilm) verbessert visuelle Effekte.
- Reinigung und Auftragen von Rahmenversiegelung : Vorbereitung für das Einsetzen der Flüssigkristalltröpfchen.
- Flüssigkristallinjektion : Präzises Verteilen der Flüssigkristalle auf dem Display.
- TFT- und CF-Laminierung : Zusammenkleben der TFT- und CF-Komponenten.
- UV-Härtung und thermische Verarbeitung : Verfestigung und gleichmäßige Verteilung des Flüssigkristalls durch ultraviolettes Licht und Wärmebehandlung.
- Schneiden, elektrische Prüfung und Kantenglättung : Formen des Substrats, Durchführen elektrischer Prüfungen und Glätten der Kanten.
- Anbringen und Entfernen von Polarisatoren : Anbringen von Polarisationsfolien und Entfernen von Luftblasen, wobei bei Bedarf eine Nacharbeit möglich ist.

- Laserschneiden und elektrische Prüfung : Sicherstellung präziser Form und elektrischer Integrität.
- COG-Bonding (Chip On Glass), FPC-Bonding (Flexible Printed Circuit) und Testen : Installieren und Testen der Treiberschaltung.
- Montage und elektrische Prüfung : Zusammenführen aller Anzeigemodulteile und Durchführen abschließender elektrischer Prüfungen.
- Alterung : Langfristige Stromversorgung zur Gewährleistung der Produktzuverlässigkeit.
- Verpackung und Versand : Vorbereitung des fertigen Produkts für die Lieferung.

Array-Segmentfluss
- G: Der Gate-Isolator aus SiNx (Siliziumnitrid) sorgt für die notwendige Isolierung zwischen dem Gate und anderen Schichten.
- I: Die Kanalschicht, a-Si (amorphes Silizium), in der die elektronische Schaltung stattfindet.
- N: Die n+ a-Si-Schicht ist mit einer hohen Konzentration an Phosphin (PH3) dotiert. Diese Dotierung reduziert die Potentialbarriere an der Schnittstelle und gewährleistet einen ohmschen Kontakt, der für einen zuverlässigen Gerätebetrieb entscheidend ist.

Gate-Metall (AlNd/MoN)

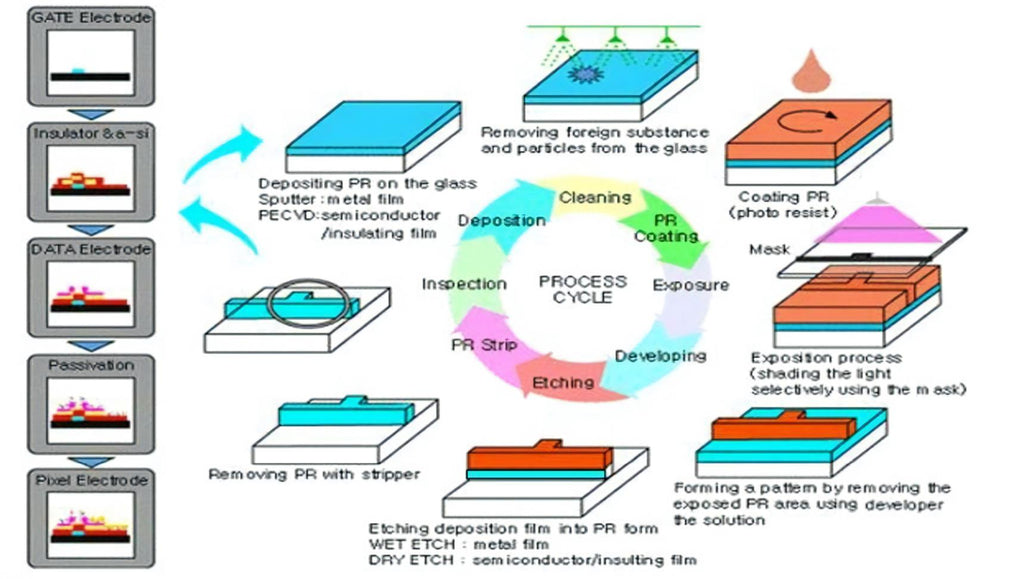
GIN (SiNx / a-Si / n+ a-Si)

S/D-Metall (Mo \Al\Mo)
Die Bildung der Source- und Drain-Elektroden (S/D), der Datenelektrode und des Kanals umfasst spezielle Verfahren wie das Auftragen von Molybdännitrid (MoN) und reinem Aluminium (für Source und Drain), das Aufsprühen der S/D-Metallschicht, S/D-Fotolithografie, S/D-Nassätzen und Kanal-Trockenätzen. Durch diese Prozesse werden die Source- und Drain-Elektroden, der Kanal und die Datenleitungen des TFT auf dem Glassubstrat gebildet. In dieser Phase ist die Konstruktion des TFT abgeschlossen. Das resultierende Design und der Prozess sind wie folgt:
- S/D-Sputtern : Dies ist ein entscheidender Schritt zur Bildung von Source-/Drain-Elektroden. Während dieses Prozesses wird durch Sputtern schwerer Metallionen auf das Substrat eine dichte Schicht aus Metallelektroden gebildet.
- Reinigung vor der PR-Beschichtung : Vor dem Auftragen des Fotolacks muss das Substrat gereinigt werden, um Staub und Rückstände zu entfernen, um gute Beschichtungsergebnisse zu gewährleisten.
- DHP (Hot Plate) : Um den Fotolack besser auf dem Substrat zu haften, wird das Substrat vor dem Beschichtungsprozess auf einer Heizplatte vorgewärmt.
- Resistbeschichtung : Auf das vorgewärmte Substrat wird eine Schicht Fotolack aufgetragen, die zur anschließenden Strukturierung verwendet wird.
- Vorhärten (SHP) : Das mit Fotolack beschichtete Substrat wird vorgehärtet, um den Fotolack gleichmäßiger und fester zu machen.
- Schrittweise Belichtung : In diesem Schritt wird die Lichtmenge gesteuert, um bestimmte Bereiche des Fotolacks zu härten und das gewünschte Muster zu erzeugen.
- Entwickeln : Der belichtete Fotolack wird verarbeitet, um das Muster sichtbar zu machen.
- Photoresist Post Baking (HHP) : Das Photoresistmuster wird durch einen weiteren Erhitzungsprozess weiter gehärtet und deutlicher hervorgehoben. Dadurch kann auch die Widerstandsfähigkeit gegen chemische Korrosion und Verschleiß verbessert werden.
- Inspektion während der Entwicklung : Nach der Entwicklung ist eine detaillierte Inspektion erforderlich, um die Genauigkeit des Musters sicherzustellen und etwaige Probleme umgehend zu erkennen und zu beheben.
- Nassätzen : Dies ist ein chemischer Reaktionsprozess, bei dem eine ätzende Flüssigkeit verwendet wird, um das Material in den ungeschützten Bereichen zu ätzen und so das Schaltungsmuster zu bilden.
- Trockenätzen von Kanälen : Zwischen Quelle und Abfluss wird ein Kanal gebildet. Bei diesem Verfahren wird das Silizium im Kanalbereich mithilfe einer Trockenätztechnik in die gewünschte Form geätzt.
- Resist-Stripping : Zum Schluss wird der Fotolack auf dem Substrat entfernt, um es zu reinigen.
Nach den obigen Schritten werden schließlich die Source-/Drain-Elektroden, Datenelektroden und der Kanal des TFT auf dem Glassubstrat gebildet.
Passivierung (SiNx)
Die Bildung der Passivierungsschicht (SiNx), oft auch als Schutzisolationsschicht bezeichnet, zusammen mit den Durchkontaktierungen umfasst spezielle Vorgänge wie die Bildung eines PECVD-Films, Photolithografie und Trockenätzen zur Erzeugung der Durchkontaktierungen. Nach Durchlaufen dieser Verfahren werden schließlich die Schutzisolationsschicht für den TFT-Kanal und die leitfähigen Durchkontaktierungen auf dem Glassubstrat gebildet. Die Bilder und der Prozess, die nach Abschluss dieser Schritte erhalten werden, sind wie folgt:
2. Reinigung vor der Beschichtung - Hier wird das Substrat vor dem Auftragen des Fotolacks gereinigt.
3. Vorbacken auf der Heizplatte (DHP) – Dabei wird das Substrat mithilfe einer Heizplatte vorgewärmt, um es für den Beschichtungsschritt vorzubereiten.
4. Fotolackbeschichtung – In diesem Schritt wird eine Schicht Fotolack auf das Substrat aufgetragen.
5. Weiches Backen (SHP) – Das mit Fotolack beschichtete Substrat wird einem Vorhärtungsprozess unterzogen, um die Schicht zu verfestigen.
6. Schrittbelichtung - Hier wird die Stepperlithografie-Technologie verwendet, um den Fotolack zu belichten und Muster zu bilden.
7. Entwicklung – Der belichtete Fotolack wird verarbeitet, um das Muster sichtbar zu machen.
8. Hart backen (HHP) – Das Fotolackmuster wird durch eine Nachbehandlung gehärtet.
9. Inspektion nach der Entwicklung – In dieser Phase wird das entwickelte Substrat überprüft, um die Genauigkeit der Muster zu bestätigen.
10. Nassätzen - Unerwünschte Dünnschichtmaterialien werden durch ein nasschemisches Ätzverfahren entfernt, um Schaltungsmuster zu erzeugen.
11. Fotolack-Stripping – Der Fotolack wird entfernt und die Substratoberfläche gereinigt.
12. Kontaktlochätzen (CH-Ätzen) – Die erforderlichen Durchkontaktierungen werden durch ein Trockenätzverfahren gebildet.
Dies sind die detaillierten Schritte zur Vorbereitung des Substrats für TFT-Anwendungen, die zum Schutz des aktiven TFT-Kanals und zur Bildung leitfähiger Durchkontaktierungen führen.
Bildung einer transparenten Pixelelektrode ITO (Indium-Zinn-Oxid)
Die Herstellung transparenter Pixelelektroden in TFT-Displays ist ein anspruchsvoller Prozess, der mit der Abscheidung von Indium-Zinn-Oxid (ITO) beginnt. Die einzelnen Schritte sind präzise ausgeführt und umfassen das Aufsprühen der ITO-Schicht, um Transparenz zu erzielen, gefolgt von Photolithografie zur Erstellung komplexer Muster und abschließend Nassätzen zur Fertigstellung der Pixelstruktur. Dieser sorgfältige Prozess endet mit der Bildung der Pixelelektroden, die perfekt auf dem Glassubstrat integriert werden und den entscheidenden Abschluss des Array-Prozesses darstellen. Der folgende Arbeitsablauf beschreibt die Verfeinerung und Abfolge der Vorgänge nach Abschluss des Prozesses.
- Pixelschichtabscheidung (ITO-Sputtern) – Bildet einen transparenten leitfähigen Film aus ITO (Indiumzinnoxid) für die nachfolgende Pixelmusterung.
- Substratreinigung (Reinigung vor der Lackbeschichtung) – Gewährleistet die Reinheit des Substrats vor dem Auftragen des Fotolackmaterials.
- Substratvorwärmung (Dehydration Hot Plate, DHP) – Bereitet das Substrat mit einem Vorbackschritt für eine optimale Fotolackhaftung vor.
- Resistauftrag (Beschichtung) – Trägt eine gleichmäßige Fotolackschicht auf das Substrat auf.
- Soft Bake (Vorhärtung SHP) – Führt eine Vorhärtung durch, um den Fotolack vor der Strukturierung zu verfestigen.
- Präzisionsbelichtung (Stepper-Belichtung) – Verwendet Stepper-Photolithografie, um den Fotolack zu belichten und so das gewünschte Muster zu erzeugen.
- Musterentwicklung (Entwicklung) – Entwickelt den belichteten Fotolack, um das komplexe Pixelmuster sichtbar zu machen.
- Resist-Härtung (Nachbelichtungsbacken, Hard Bake HHP) – Härtet den gemusterten Fotolack, um die Ätzbeständigkeit zu verbessern.
- Musterinspektion (Inspektion nach der Entwicklung) – Überprüft die entwickelten Muster auf Genauigkeit und Integrität.
- Musterübertragung (ITO-Ätzung) – Überträgt das Muster durch Ätzen der ITO-Schicht, um Pixelelektroden zu bilden.
- Resistentfernung (Streifen) – Entfernt den Fotolack und hinterlässt eine saubere Substratoberfläche.
- Leistungssteigerung (Annealing) – Glühen der Komponenten, um die elektrischen Eigenschaften der Dünnschichttransistoren zu verbessern.
- Qualitätskontrolle (TEG-Test) – Führt elektrische Tests an Testelementen durch, um die Qualität während der Produktion zu überwachen.
Diese optimierte Abfolge legt den Grundstein für hochwertige TFT-Displays mit optimaler elektrischer Leistung.

Farbfilter (CF)-Verfahren
- Glassubstrat: Die grundlegende Basisschicht, die mechanischen Halt bietet.
- Schwarze Matrix (BM): Es besteht aus einem lichtabsorbierenden Material, grenzt jedes Pixel ab und minimiert den Lichtverlust zwischen den Pixeln, wodurch der Kontrast verbessert wird.
- Farbige Harzschichten: Als eigentliche Rot-, Grün- und Blaufilter bestimmen diese Schichten die Pixelfarben. Sie bestehen aus einem durchgefärbten, transparenten Harzmaterial.
- Überzugsschicht (OC): Eine Schutzschicht über den Farbharzen gleicht die Oberfläche aus und schützt die Filter vor physikalischen und chemischen Schäden.
- ITO-Elektrode (Indiumzinnoxid): Diese transparente, leitfähige Schicht ermöglicht es dem Panel, als Elektrode zu fungieren und das hindurchtretende Licht zu regulieren.

- Untergrundvorbereitung: Die Sauberkeit des Glassubstrats hat höchste Priorität, daher wird es gründlich gereinigt, um Verunreinigungen zu beseitigen, die die CF-Qualität beeinträchtigen könnten.
- Bildung der schwarzen Matrix: Durch Auftragen einer Fotolackschicht auf das gereinigte Substrat wird mithilfe der Fotolithografie das BM-Muster umrissen. Nach der Belichtung werden unentwickelte Bereiche freigelegt und mit schwarzem Pigment gefüllt, anschließend wird ausgehärtet.
- Farbharz-Anwendung: Das sukzessive Auftragen von roten, grünen und blauen Farbharzen innerhalb der BM-Grenzen erfolgt mit einem eigenen Photolithografieverfahren für jede Farbschicht. Nach dem Beschichten und Belichten werden die Bereiche ohne Fotolack entwickelt und mit dem Harz gefüllt, worauf das Aushärten folgt.
- Auftragen der Deckschicht: Auf die Harzfarben wird eine OC-Schicht aufgetragen, um sie zu schützen und eine glatte Oberfläche für die nachfolgende ITO-Elektrodenabscheidung zu schaffen.
- ITO-Elektrodenabscheidung: Die transparente ITO-Elektrode wird durch Sputtern auf die OC-Schicht aufgebracht und anschließend gemustert, um die Elektrodenarchitektur zu strukturieren.
- Inspektion und Prüfung: Während der gesamten Produktion wird die CF-Qualität durch sorgfältige Kontrollen und Tests sichergestellt. Kennzahlen wie Farbtreue, Einheitlichkeit und Fehlerniveau werden gründlich geprüft.
- Integration: Nach der Qualitätssicherung wird der Farbfilter präzise ausgerichtet und mit Bestandteilen des TFT-LCD-Panels wie dem TFT-Array und der Flüssigkristallschicht laminiert.

CELL-Segmentfluss
Der Produktionsprozess im Bereich „Zelle“ eines TFT-Displays kann grob in vier Hauptphasen unterteilt werden: Ausrichtung, Boxen, Schneiden und Anbringen des Polarisators. Die Ziele und Hauptverfahren dieser Phasen werden im Folgenden kurz umrissen:
Der Ausrichtungsprozess
Ziel des Ausrichtungsprozesses ist es, eine Schicht aus transparentem PI-Film (Polyimid) auf den TFT- und CF-Substraten zu erzeugen. Durch einen anschließenden Reibungsprozess beeinflusst diese Schicht die Ausrichtung der Flüssigkristallmoleküle in Reibungsrichtung. Für ein tieferes Verständnis der zugrundeliegenden Prinzipien sollten interessierte Leser die entsprechende Literatur zu Rate ziehen. Daher werden in dieser Phase vor allem zwei Hauptprozesse behandelt: PI-Druck und Reiben.
PI (Polyimid)-Druck
Polyimid (PI) ist ein hochleistungsfähiges, transparentes organisches Polymermaterial, das aus Haupt- und Seitenketten besteht. Nach dem Auftragen und Backen haftet es fest auf den Oberflächen von CF- und TFT-Substraten. Die Beschichtung von PI erfolgt mithilfe einer speziellen Tiefdrucktechnik. Neben dem primären Tiefdruckprozess umfasst der PI-Druck mehrere Zusatzprozesse, darunter die Substratreinigung vor dem Drucken, das Vorbacken nach dem Drucken, die automatische optische Inspektion, das Aushärten sowie bei Bedarf einen PI-Nacharbeitsprozess.
1. Reinigung vor dem PI : In diesem Schritt wird der Untergrund vor dem Drucken gründlich gereinigt, um sicherzustellen, dass er frei von Staub, Fett und anderen Verunreinigungen ist, um ihn für die nächsten Schritte vorzubereiten.
2. PI-Druck : Hierbei wird das PI-Material (Polyimid) auf das Substrat aufgetragen, analog zum Drucken eines Designs auf Papier, mit dem Unterschied, dass die „Tinte“ ein spezielles Material ist, das eine Schutzschicht bildet.3. Vorbacken : Betrachten Sie dies als eine vorläufige Backphase, in der die PI-Schicht teilweise trocknet, um eine ordnungsgemäße Haftung auf dem Substrat sicherzustellen.
4. PI-Inspektion : An diesem Punkt werden die gedruckten Schichten einer genauen Untersuchung auf Flecken, Unebenheiten oder Mängel unterzogen, vergleichbar mit der Untersuchung einer gestrichenen Wand auf Unvollkommenheiten.
5. PI-Nacharbeit : Wenn bei der Inspektion Probleme festgestellt werden, müssen in diesem Schritt diese Mängel behoben werden, ähnlich wie beim Entfernen von Fehlern in einer Skizze.
6. PI-Härtung : Schließlich wird die PI-Schicht durch einen Backvorgang vollständig ausgehärtet, ähnlich wie Ton in einem Ofen ausgehärtet wird, wodurch sie stark und haltbar wird.
In diesem Schritt werden Staub und Partikel mithilfe eines Ultraschallreinigers vom Substrat entfernt. Dieser verwendet Ultraschallwellen für eine gründliche Reinigung. So wird sichergestellt, dass das Substrat frei von Verunreinigungen ist, bevor mit den nächsten Schritten fortgefahren wird.
2. Ausrichtung:
In der Ausrichtungsphase wird die Ausrichtung des Substrats angepasst, um visuelle Anforderungen zu erfüllen. Dieser Prozess ist unkompliziert und konzentriert sich auf die korrekte Positionierung des Substrats für nachfolgende Behandlungen.
3. Reiben:
Beim Reiben wird mit einem Samttuch über die PI-Schicht gerieben. Dadurch werden die Seitenketten des PI in eine einheitliche Richtung ausgerichtet und die Molekülstruktur so organisiert, dass die gewünschten Oberflächeneigenschaften erzielt werden.
4. Ultraschallreinigung nach dem Reiben (USC):
Nach dem Reiben können sich auf dem Substrat Partikel oder Rückstände befinden. Die USC-Reinigung nach dem Reiben entfernt diese Rückstände und sorgt dafür, dass die Oberfläche des Substrats makellos sauber ist. Dieser Schritt ist entscheidend für die Aufrechterhaltung der Qualität des Endprodukts, da dabei Ultraschallwellen verwendet werden, um alle während des Reibvorgangs anhaftenden Partikel oder Rückstände zu lösen und zu entfernen.

ODF (One Drop Fill)-Verkapselungsprozess
1. Auftragen von Dichtungsmittel und Silberpaste: Als Dichtungsmittel wird UV-härtender Klebstoff verwendet, der entlang der Kanten der CF- und TFT-Glassubstrate aufgetragen wird, um sicherzustellen, dass die beiden Substrate fest miteinander verbunden sind und um die Dicke der Zelle zu definieren. Gleichzeitig dient das Auftragen von Silberpaste zum Verbinden der gemeinsamen Elektroden auf CF und TFT, um die elektrische Konnektivität sicherzustellen.
2. Flüssigkristallbeschichtung: Flüssigkristallmaterial wird auf das TFT-Substrat getropft, das bereits mit dem Dichtungsmittel beschichtet wurde. Das Flüssigkristallmaterial spielt eine entscheidende Rolle im Anzeigeprozess. Es passt den Zustand des durchdringenden Lichts an, indem es seine Anordnung ändert, und steuert so die Farbe und Helligkeit der Pixel.
3. Vakuumverbindung: Das mit Dichtungsmittel, Silberpaste und Flüssigkristall beschichtete CF-Substrat wird in einer Vakuumumgebung mit dem TFT-Substrat verbunden. Dieser Schritt hilft, die Bildung von Blasen zu verhindern und stellt sicher, dass eine dichte, lückenlose Verbindung zwischen den beiden Substraten besteht.
Thermische Aushärtung: Nach Abschluss der UV-Härtung werden die Substrate einem thermischen Prozess unterzogen, um die Haftung des Dichtungsmittels weiter zu stärken. Dieser Schritt zielt insbesondere auf Bereiche ab, die nicht vollständig vom UV-Licht erreicht werden, wie z. B. unter den Leitungen, und stellt sicher, dass diese Teile vollständig ausgehärtet werden.

1.Schneiden
Aufgrund der bestimmten Größe des Glassubstrats und der Vielfalt der Produktgrößen werden mehrere Produktzellen auf einem einzigen Glassubstrat angeordnet. Das Schneiden erfolgt, indem eine Diamantscheibe über die Glasoberfläche gleitet. Normalerweise erfolgt nach dem Schneiden ein Enthaftungsprozess, aber dank der Fortschritte in der Schneidscheibentechnologie gibt es jetzt eine Technik, die eine sehr tiefe Schnittspur erzeugt, wodurch die Enthaftung überflüssig wird.
2.Kanten
Nachdem das Glas in einzelne Bildschirme geschnitten wurde, weisen die Kanten jedes Bildschirms viele feine Risse auf. Um zu verhindern, dass diese Risse bei der anschließenden Handhabung durch Kollisionen zu Brüchen führen, ist eine Kantenbehandlung erforderlich.
3.Elektrische Messung
Die elektrische Messung ist ein Hilfsprozess, der während der Produktion mehrmals verwendet wird. Hier ist sie jedoch besonders wichtig, da hier zum ersten Mal Elektrizität angewendet wird, um die Anzeigeleistung des LCD zu testen. Das Testprinzip ist einfach: Einzelne Anzeigepixel werden mit Elektrizität versorgt und die Anzeigeleistung der Zelle wird durch einen Polarisationsfilm beobachtet. Normalerweise wird ein kurzer Balken, der für Array-Tests verwendet wird, mit Elektrizität versorgt. Nach der elektrischen Prüfung werden Bildschirme, die den Standards nicht entsprechen, entfernt, um Materialverschwendung in späteren Phasen zu vermeiden.
Zu den zusätzlichen Hilfsprozessen gehören die Sichtprüfung nach dem Schneiden und die Reinigung nach der Kantenbearbeitung.
Montageprozess für TFT-Anzeigemodule
Zu den wichtigsten Prozessen bei der Montage von TFT-Displaymodulen gehören das Aufbringen der Polarisationsfolie, COG- und FPC-Verbindungen, die Montage und verschiedene unterstützende Prozesse. Nachfolgend finden Sie eine detaillierte Einführung zu jedem Prozess:
1.COG- und FPC-Verbindung
COG (Chip on Glass) und FPC (Flexible Printed Circuit) sind Methoden zum Verbinden von Schaltkreisen. Aufgrund der Vielzahl an Elektroden sind herkömmliche Eins-zu-eins-Drahtverbindungen eine Herausforderung. Die derzeitige Praxis besteht darin, ein Elektrodenarray auf dem Glas mit einem entsprechenden Array auf dem IC/FPC zu bilden und mithilfe eines anisotropen leitfähigen Films (ACF) jede IC/FPC-Elektrode nacheinander mit der Glaselektrode zu verbinden.2.Aufbringen der Polarisationsfolie
Da der LCD-Betrieb auf polarisiertem Licht basiert, ist die Anbringung einer Polarisationsfolie ein wesentlicher Vorgang. Diese Folie steuert das Licht, das durch die Flüssigkristallzellen hindurchtritt, um Bilder zu erzeugen.
3.Montage
Bei der Montage werden Hintergrundbeleuchtung, Bildschirm, Steuerplatine und andere Komponenten wie Touchscreens zu einem vollständigen Displaymodul zusammengefügt. Dies geschieht normalerweise manuell durch qualifizierte Techniker, die eine entscheidende Rolle bei der Sicherstellung der Qualität der zusammengebauten Module spielen.
Der Modulbereich umfasst neben den Hauptprozessen auch zahlreiche Hilfsprozesse, wie zum Beispiel:
1. Laserschneiden und elektrische Messungen nach dem Schneiden
Nachdem die Komponenten mit einem Laser präzise geschnitten wurden, werden ihre elektrischen Funktionen getestet, um sicherzustellen, dass sie die erforderlichen Spezifikationen erfüllen.2. Elektrische Messungen während und nach dem Bonden
Nach den COG- und FPC-Bonding-Prozessen werden auch elektrische Tests durchgeführt, um die Integrität dieser Verbindungen zu überprüfen.
3. Mikroskopische Inspektion
Nach dem Laserschneiden und -verbinden werden mikroskopische Inspektionen (oder eine Automatische Optische Inspektion (AOI) beim FPC-Verbinden) durchgeführt, um nach Defekten oder Problemen zu suchen.
4. Schälfestigkeitstest
Nach dem IC-Bonding und FPC-Bonding werden Abzugsfestigkeitstests durchgeführt, um die Haltbarkeit der Bindungen zu bewerten.
5. Alterung nach der Montage
Um eine langfristige Zuverlässigkeit zu gewährleisten, werden die montierten Module einem Alterungsprozess unter Spannung unterzogen.
6.Verpackung und Versand
Sobald die Module alle Tests und Prüfungen bestanden haben, werden sie verpackt und an den Kunden oder die nächste Produktionsphase versandt.

Hinterlasse einen Kommentar
Diese Website ist durch hCaptcha geschützt und es gelten die allgemeinen Geschäftsbedingungen und Datenschutzbestimmungen von hCaptcha.